Geben Sie Ihren bestehenden Geräten eine zweite Leben!
Wir renovieren und rüsten Ihre Ausrüstung auf, um den aktuellen Standards zu entsprechen, und gewährleisten die Einhaltung und Leistung, die mit einer neuen Einheit vergleichbar ist. Unsere renovierten Geräte bieten die gleiche Garantie wie neue Geräte und bieten Ihnen Zuverlässigkeit und Sicherheit. Maximieren Sie die Lebensdauer Ihrer Ausrüstung, während Sie von einer kostengünstigen und nachhaltigen Lösung profitieren!
Interventionen an allen Arten von Geräten
Nach jahrelangem Einsatz muss einige Ausrüstung möglicherweise renoviert werden. Wenn Sie Geräte haben, die für eine Renovierung in Frage kommen, können Sie sich auf uns verlassen, um jeden Schritt des Zyklus zu übernehmen (Demontage, Renovierung und Aufrüstung in unseren Werkstätten, Installation und Inbetriebnahme), um Ihnen ein brandneues Gerät zu liefern.
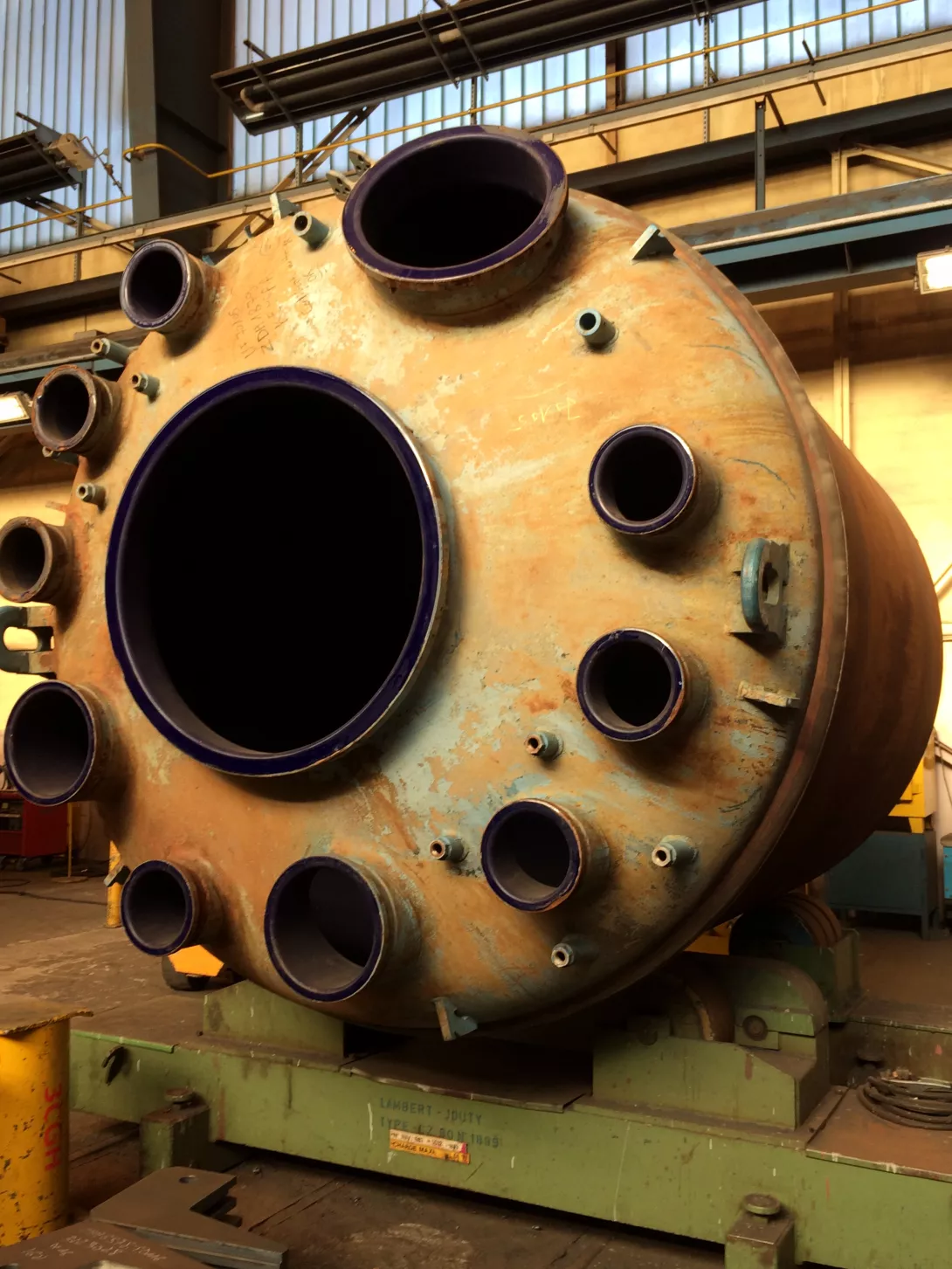
Vitrifizierte Geräte Aufrüstung und Renovierung
Alle vitrifizierten Reaktoren, Kolonnen und Zubehörteile wie Abdeckungen, Rührwerke und Baffeln können neu verglast werden, wenn das Stahlsubstrat in reparierbarem Zustand ist. Das Neuverglasen ist der Prozess, bei dem ältere oder beschädigte vitrifizierte Stahlgeräte in einen neuwertigen Zustand versetzt werden. Dieser Vorgang wird in den nächstgelegenen De Dietrich Einrichtungen durchgeführt, wobei die Einhaltung der Industriestandards sichergestellt wird. Dort können die Geräte auch mit fortschrittlichen Technologien, Designänderungen oder Verbesserungen des Heizsystems aufgerüstet werden. Wir können alle Geräte neu verglasen, unabhängig davon, ob sie von De Dietrich oder anderen Lieferanten hergestellt wurden.
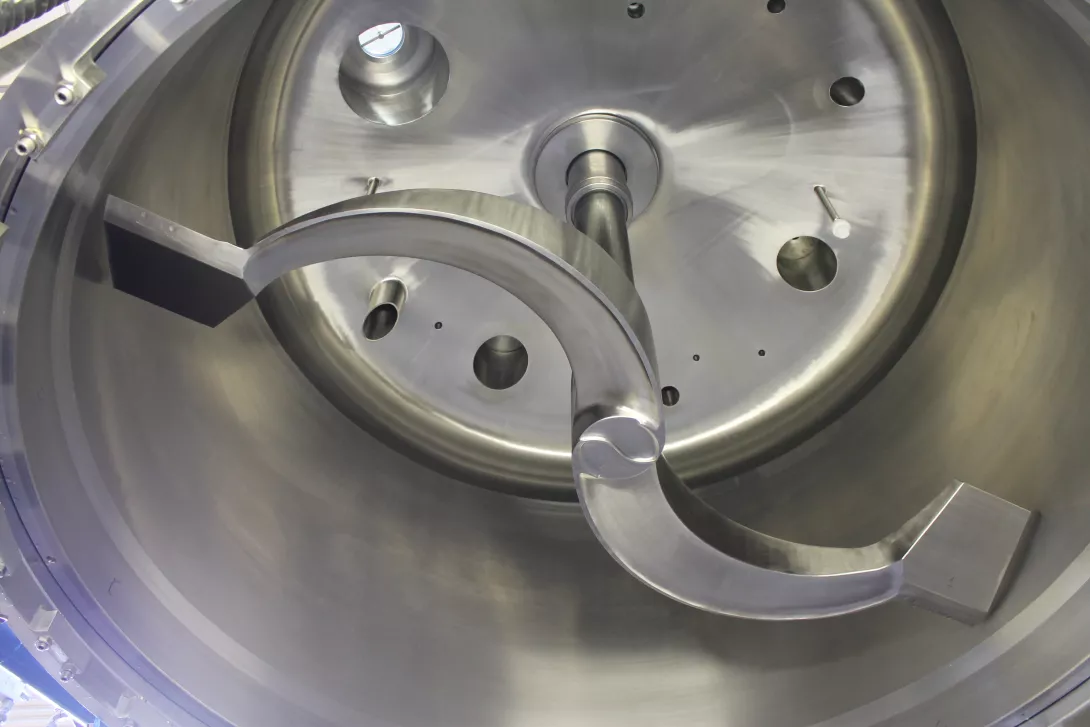
Ausrüstungsaufrüstung und Renovierung von Legierungen
Alle Geräte in unserem Produktportfolio können aufgerüstet und renoviert werden, einschließlich Filtertrockner, Trockner, Zentrifugen, Reaktoren und Kolonnen. Wir verlängern die Lebensdauer Ihrer Ausrüstung und integrieren die neuesten Technologien für eine verbesserte Leistung. Wir rüsten auch Geräte anderer Hersteller mit unseren patentierten, branchenführenden Lösungen auf.
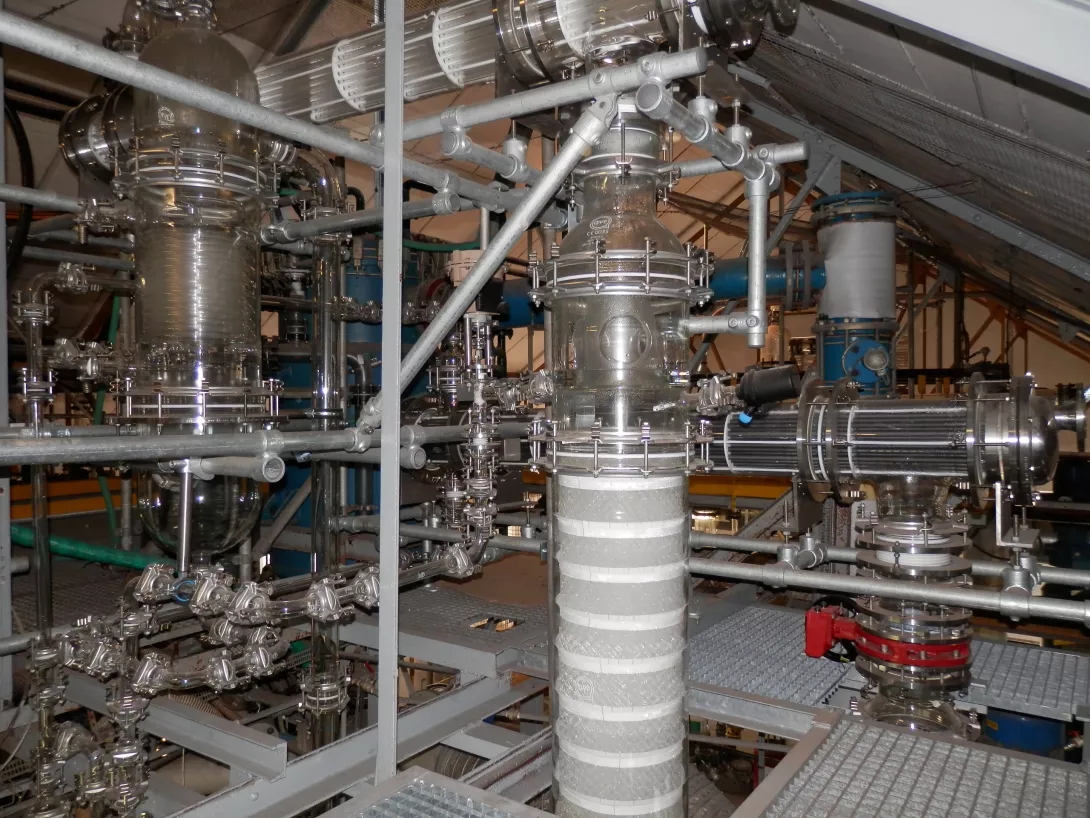
Reparatur von Glasgeräten
Komplette Renovierung Ihrer Ausrüstung, Austausch von Dichtungen und Zubehör, Messung der Glasdicke. Wir können Ihre Ausrüstung auf den erforderlichen Standard bringen, um die erforderlichen Normen/Zertifizierungen (Atex, FDA, ...) zu erfüllen.
Highlights der Aufrüstung & Modernisierung
...
Wirtschaftliche Lösung & verkürzte Lieferzeiten
Möglichkeit, Ihre alte Apparatur aufzurüsten bei gleicher Garantie wie für neue Geräte
Neue Dokumentationen und Bescheinigungen
Intervention bei allen Marken von Apparaturen
Hast du Fragen?
Unsere Teams sind bereit, mit dir zusammenzuarbeiten und Lösungen für deine Projekte anzubieten.