Bringing New Life to your Old Glass-Lined Reactor through Reglassing
Description
Glass-lined steel reactors are a substantial investment for any company to make, so it’s not the kind of equipment you want to simply discard once it becomes old or inoperative.
Glass-lined steel reactors are a substantial investment for any company to make, so it’s not the kind of equipment you want to simply discard once it becomes old or inoperative. Most likely, you are using glass-lined equipment because your process requires a high level of corrosion resistance or other unique property that only glass lining can provide. But after years of service (the number of years can vary greatly depending on the service conditions), your vessel will eventually require some sort of refurbishment. Damage from mechanical or thermal shock can also prematurely cause your vessel to be out of commission, but in most cases when operating guidelines are followed, normal wear and tear will be the cause of erosion to the glass lining.
Fortunately, there is a simple and economic solution to salvage your existing vessel and make it usable again, even to the point of “like-new” condition. It sounds too good to be true, right?! But it’s not – reglassing is an economical alternative to purchasing new equipment. Here we’ll define the five Ws and one H to give you a clearer understanding of reglass service and how it can work for you.
WHAT IS REGLASSING?
Reglassing is a complex process that provides efficient, cost-effective repair to old, damaged or worn glass-lined vessels and their accessories, such as agitators, baffles and covers. Once a vessel or ancillary part is reglassed it is equivalent in quality to a new item. The reglassing procedure involves the following steps:
- Removal of the old glass lining from a vessel or part by grit-blastin
- Repair of the steel substrate by welding (e.g. stud holes from plugs and corrosion-damaged areas are ground out and patch welded, severely corroded sections may be trepanned and a new section welded in)
- Addition or removal of nozzles or other changes (such as replacement of jacket closure rings or addition of diaphragms)
- Application and firing of numerous coats of glass
- Testing before and after glassing
- Application of external protective coatings
WHEN MIGHT YOU NEED TO HAVE YOUR VESSEL REGLASSED?
Reglassing may not be practical for an older vessel if there is significant corrosion of the steel surfaces. But if the steel substrate is in good condition, reglassing is most likely a viable option for you. Some scenarios, in addition to basic erosion of the glass lining, that can warrant the need for reglass service include:
- galvanic corrosion caused by the use of dissimilar metals in the reactor, like dip pipes, valves and/or repair plugs.
the loss of a repair plug. - temporary build-up of extremely corrosive or erosive products from batch type operations and pilot operations.
- contamination of jacket heating and cooling media (which can accelerate corrosion at the bottom closure ring).
- lack of venting, which can allow corrosion-producing air pockets at the top jacket closure ring.
- damage caused by a component that is welded to the substrate.
- accidental mechanical damage to the lining of the vessel (e.g. dropping a tool or other object into the vessel).
- thermal shock or stress beyond the safe limits of the glass (when operating limitations are exceeded or temperature differentials are not adhered to).
WHERE DO YOU SEND YOUR EQUIPMENT TO BE REGLASSED?
Finally you are ready to ship your equipment to the vendor you’ve selected to perform your reglass service. If you are working with DDPS, unless otherwise advised, your equipment can be shipped to our Zinswiller facility at the following address:
De Dietrich Process Systems
30 Grand Rue, 67110 Zinswiller
FRANCE
When your equipment is returned to you it will come with the same standard warranty as new vessels so you can be assured you’ll have superior quality equivalent to what you would expect from a brand new vessel or part.
DDPS offers affordable reglassing services on our own vessels as well as on many other vendors’ equipment. Even if you’re unsure if your equipment qualifies for reglassing, it’s an affordable solution worth looking into. For a complimentary quote, contact us so we can better assess if this is an economical choice for you to consider.
WHY IS REGLASSING A GOOD OPTION?
There are many advantages in choosing to reglass a vessel, but the primary ones are time and money. From a cost perspective, because the carbon-steel pressure vessel is being salvaged, the cost to reglass a vessel is often less than half of what the vessel would be to purchase “new”. (The re-use of the vessel also fits well with many corporate sustainability programs.) Deliveries for reglassed equipment typically run two to three months – again, approximately half the time it takes to fabricate a new vessel from scratch. And some companies (like DDPS, for example) offer a warranty on the reglassing work that is equivalent to the one you get with new equipment purchases!
In addition to the time and money savings, you can use the reglassing process to make minor changes to nozzle layouts, add updated features like Optimix® baffles or factory-installed insulation and sheathing, or a variety of other changes to improve the functionality and appearance of your existing equipment.
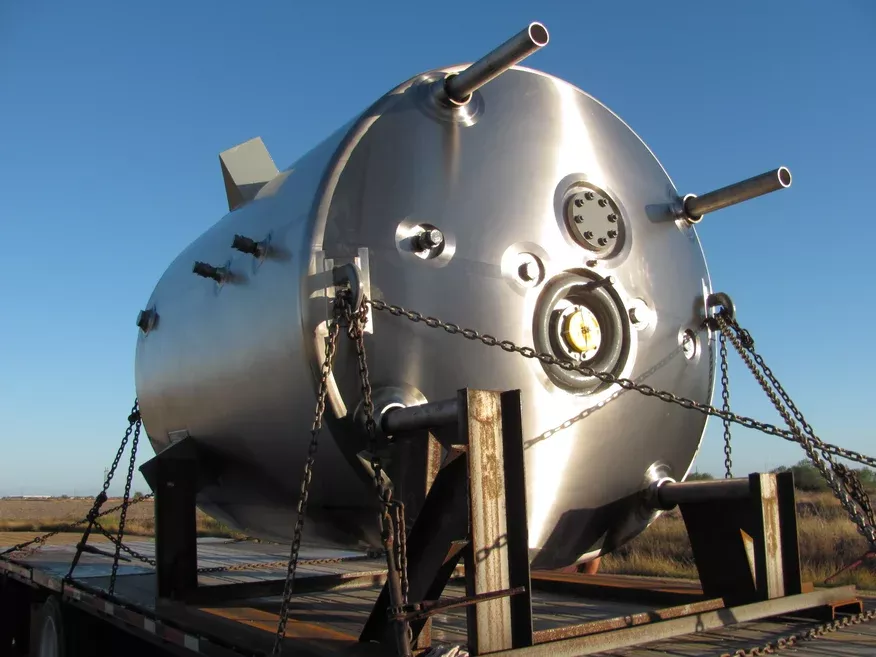
WHO DETERMINES IF YOUR VESSEL IS A CANDIDATE FOR REGLASSING?
Before you go to the expense of shipping, it’s best to “pre-qualify” the vessel on-site. A representative from the reglassing vendor of your choice should inspect the vessel with you. First you’ll need to remove accessories and disassemble the vessel as required to inspect the glass, and make a preliminary evaluation as to the possibility of reglassing. If the vessel seems in “reglassable” condition, you can follow the steps outlined by the vendor to prepare and ship the vessel.
HOW DO YOU PREPARE YOUR VESSEL FOR REGLASSING?
Once you’ve decided that your equipment is a candidate for reglassing these are the steps you should following for preparing your equipment to send in for service:
- Clean exterior and interior of the vessel
Many processes involve toxic, flammable, or irritating constituents. It is essential that the vessel be thoroughly cleaned, so that it is free of product residue and contaminants, especially those which may generate flammable or toxic fumes when heated. Reactor jackets need to be cleaned thoroughly as well. - Remove all insulation and accessories
Exterior insulation must be removed prior to shipment. Insulation clips, rings, studs, etc. do not need to be removed. All accessories not subject to repair or replacement, such as the drive and agitation system, all split flanges and clamps, baffles, piping, fittings, instrumentation, and so on should be removed. The bare vessel should be shipped as one item; accessories like agitators and baffles should be removed and shipped separately from the bare vessel. You can contact your reglassing vendor for clarification if you have any doubts as to what should and shouldn’t be removed. - Prepare your vessel for shipment
Properly position and fasten the vessel, and any accessories, on sturdy shipping skids. If any special handling is required, be sure to notify the carrier and DDPS, and mark papers accordingly. Be sure to identify your equipment, including your company name and address, your vessel number and location and affix it to the vessel or skid.