The Importance of Reliable Bottom Outlet Valves for Vessels
Description
A bottom outlet valve is one of the most critical components of your vessel. Just ask someone who has had a valve leakage issue and they can tell you what substantial problems it can create for your plant!
If you are reading this post, chances are you have a valuable product in that is being processed in a specialized system. When your company has made a significant expenditure on equipment, it’s only natural to want to ensure it is correctly operated and well maintained. Just as “a chain is only as strong as its weakest link”, a valve is essentially a link in the system’s “chain”. You can have a top-of-the-line vessel but if the other parts that make up the system are subpar, it will jeopardize the integrity of your entire process.
A bottom outlet valve is one of the most critical components of your vessel. Just ask someone who has had a valve leakage issue and they can tell you what substantial problems it can create for your plant! Knowing what options are out there for bottom outlet valves will help you make a more informed choice when accessorizing your reactor.
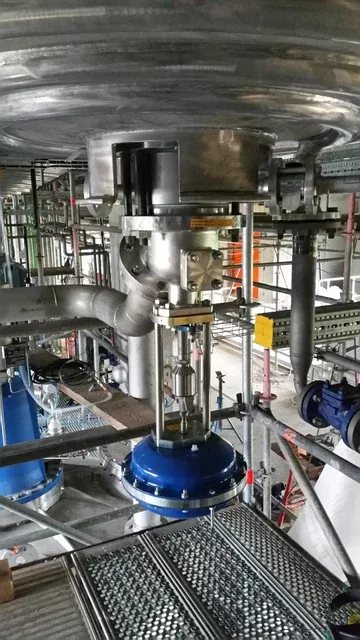
HOW IS A CLEAN VALVE DIFFERENT FROM AN ORDINARY BOTTOM OUTLET VALVE?
In addition to choosing the right material of construction, another concern when selecting a bottom outlet valve is the housekeeping factor. This is especially true in the case of batch processes that might involve a changeout of product which prohibits cross contamination. Dismantling a valve to ensure thorough cleaning between batches is a lengthy process that can create a considerable amount of unwanted downtime in production, not to mention labor (time and expenses). Our Clean Valve is uniquely designed with an additional side nozzle to allow a cleaning lance to be inserted, enabling the valve to be meticulously cleaned without removing it from service.
De Dietrich Process Systems specializes in providing bottom outlet valves that are used in various fine chemical, petrochemical, agrochemical, pharmaceutical, and biotech applications to complement our range of glass and glass-lined reactors and tanks. We also manufacture stainless steel and specialty alloy valves to comply with the drainage and cleanability demands of alternative vessel materials. The Clean Valve along with applicable spare parts is available in all of the above mentioned build materials in a variety of sizes and types (manual or pneumatic). To see the Clean Valve in operation and learn about the other enhancements available for glass-lined reactors, don't hesitate to reach out to us!
WHAT’S SO IMPORTANT ABOUT A BOTTOM OUTLET VALVE?
Bottom outlet valves, also referred to as flush valves or BOVs for short, are important for a few reasons. Fundamentally, they manage the quantity, direction and speed of material flow. They also allow you to handle media that is under high pressures and temperatures safely. Their location at the bottom of the vessel enables complete drainage of the vessel’s contents. This dead-space-free design that allows you to remove all the product at the end of a batch is not only important for cleanliness; in many cases the product is extremely valuable (think fine chemicals and pharmaceuticals) so even small quantities that can be salvaged can increase your profitability.
WHAT TYPE OF VALVE SHOULD YOU GET FOR YOUR VESSEL?
You most likely picked a material of construction for your reactor or tank that is necessitated by your product characteristics and process requirements. Depending on your specifications, this can be anything from carbon steel, stainless steel, or PTFE to more exotic metals such as nickel alloy, Hastelloy, and titanium, or glass-lined steel for particularly corrosive applications. It is critical for the safety of your process that the material of your valve matches that of the vessel it is installed on. For example, if you use a glass-lined steel vessel because of a corrosive product that is not compatible with metals or plastic polymers, you must use a glass-lined valve. After all, you don’t want what’s going through your valve to go through your valve!