Jacket Care and Cleaning Options for Glass-Lined Reactors
Description
If you work in pharmaceutical or fine chemical production you are probably well aware of the corrosion resistance, cleanability, and other qualities of glass-lined reactors that make them a necessity in your manufacturing facility.
There are many other applications that involve aggressive reaction environments, not limited to these industries, which require the unique traits of glass lining to effectively carry out their processes in order to not compromise product purity through the exposure to metal.
In fact, glass lining protects the base metal of a reactor so effectively that corrosion will usually occur in another area that all too often goes unnoticed – the reactor jacket. Although the heat transfer fluids used in the jacket space are relatively mild (especially in comparison to the contents inside the reactor itself), they will generally attack the jacket as well as the reactor exterior long before the glass-lined interior becomes damaged. Known as jacket space corrosion, this phenomenon occurs when glass-lined reactor jackets are neglected until fouling problems arise.
And what exactly is fouling? The word itself sounds terrible and dirty, doesn’t it? It certainly is not a term that has me envisioning fields of flowers or sweet little newborn puppies. Fouling, as defined by Wikipedia, is “the accumulation of unwanted material on solid surfaces to the detriment of function.” So what does this mean in terms of reactor jackets and process functionality? Iron oxide corrosion, the most common form of jacket fouling, results in prolonged heating and cooling times, a reduction in product quality, and equipment deterioration, all of which lead to an overall decrease in productivity by as much as 15%.
From the standpoint of corrosion (usually via steam condensate) and deposition (thanks to all the dissolved materials like calcium, magnesium, silica, and iron contained in the plant service water that is frequently used for cooling fluid), technology is available to control their effects and minimize the jacket damage, but it is not often proactively implemented. In the interest of extending the life of your vessel it is critical to:
Select the right type of jacket and thermal fluids based on the heating and cooling requirements of your application
Take proper care of your jacket interior to avoid scale buildup (among other problems) which can limit the flow and effectiveness of your heating/cooling fluid.
Let’s look at jacket care and the various methods of jacket cleaning that are available.
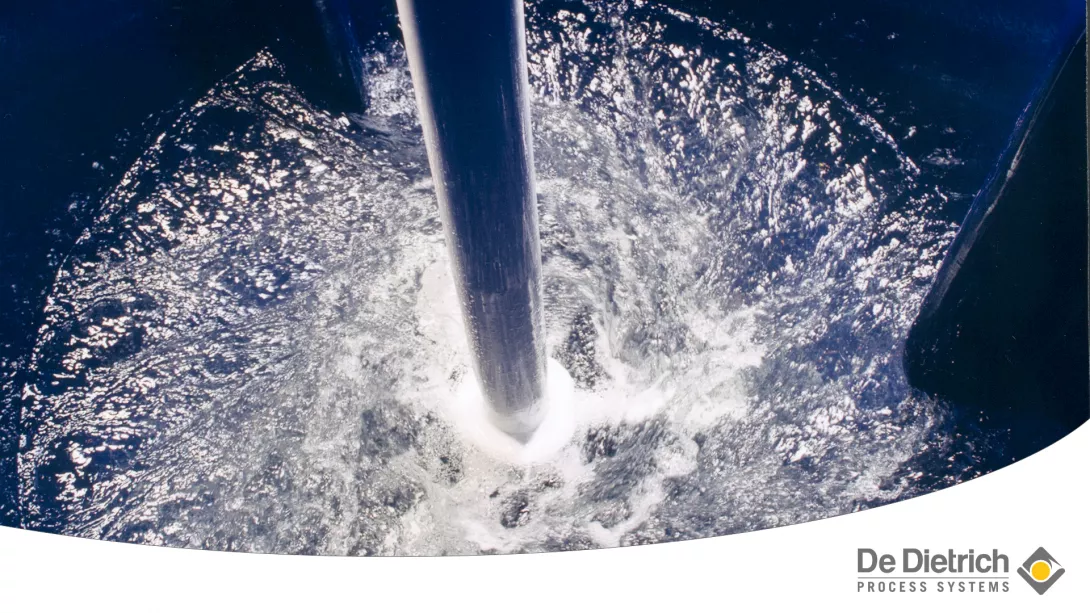
Selecting Thermal Fluids
With regard to choosing heating and cooling fluids, here are some best practices that you can follow to help offset corrosion:
Water should be treated to remove impurities and should contain a corrosive inhibitor.
Brine may be used for cooling, but must be kept at a neutral pH (the recommended brine concentrations should have a specific gravity of 1.2 and a pH of 8.0 – 8.5).
Never use brine alternately with steam or hot water. This can result in a highly corrosive condition.
Ammonia, glycerol, ethylene glycol, etc., may be used as alternate coolants or heat transfer fluids
Never use ammonia alternatively with steam or hot water
Some coolants may decompose to acid component when exposed to heat/steam, leading to corrosion of both the vessel and jacket steel. This type of attack could potentially cause a glass lining failure due to nascent hydrogen dispersion.
Preventative Maintenance
Periodic inspection of the jacket is an important examination to add in your maintenance regimen if it’s not already included. A regularly scheduled analysis will help to extend the life of your vessel (and only DDPS provides one or more jacket clean-out ports specifically for this purpose!).
DDPS jacketed vessels are equipped with a vent coupling at the top of the jacket shell and a drain coupling in the lower jacket expansion diaphragm near the vessel outlet. The recommended practice is to connect the top vent line with a valve and vent whenever liquid is first injected into the jacket. This removes all air and permits full heat transfer. It also prevents corrosion of the upper closure. The diaphragm drain should be opened at least once a week during operation to clean out all accumulated deposits and periodically “blown down” to remove sludge from the expansion ring, to prevent premature failure due to corrosion.
When it is determined that the jacket must be cleaned due to mild fouling (especially due to brine usage), we recommend a 15% solution of sodium hypochlorite (see our Glass-Lined Equipment Maintenance Manual for more information on jacket capacities). After cleaning, all jacket-agitating nozzles should be inspected and replaced if needed. There are cases, however, when fouling is moderate to severe and more aggressive action needs to be taken.
Acid Cleaning
Acid-based cleaning methods have been the conventional way to treat jacket space corrosion, but this technique does not solve the problem with fouled reactors. Acids can easily damage or destroy the internal glass lining of reactors. During acid cleaning hydrogen atoms can permeate the steel from the jacket site and react to form molecular hydrogen. This reaction results in “fishscaling”, a term used to describe the crescent-shaped chips that are created by the pressure put on the glass lining. This fishscale damage extends from the substrate metal through the glass coating to the surface, completely compromising the corrosion resistance integrity of the glass lining. DDPS advises to never use acid solution, inhibited or otherwise for cleaning jackets of glass-lined equipment.
Alkaline cleaning can be performed and is much safer on a vessel than acid cleaning, however, alkaline cleaning products have shown in practice to have little effect on the mineral scale which needs to be removed to restore heat transfer efficiency. Additionally, many other common cleaning chemicals have been proven to be ineffective against iron deposits.
pH-Neutral Cleaning
The ReStor program, developed by Ondeo Nalco Company and tested and approved by DDPS, is a service that safely cleans and restores glass-lined process reactors. The proprietary neutral pH cleaning compound GLRx™ works to quickly and safely remove iron oxide build-up from jacket interiors without damaging the glass lining or dissolving the base metal of reactors. Different service packages are available, depending on your budget and level of your involvement:
Level 1: Analysis and Consultation Option
The Ondeo Nalco and DDPS team of experts analyzes the contaminants in your reactor jacket and lays out a plan of action. We then deliver the necessary amount of cleaning compound GLRx, consult with your staff and provide written cleaning instructions to enable you to perform the cleaning in-house.
Level 2: Monitoring Option
In addition to Level 1 services, the Ondeo Nalco and DDPS team provides on-site testing and inspection services to monitor the cleaning progression. This allows you to focus on the mechanics of cleaning.
Level 3: Turnkey Option
Our team of experts takes complete responsibility for the cleaning of your equipment from our pre-site visit to completion. We supply the manpower, equipment and cleaning product necessary to restore the heat transfer efficiency of your equipment and improve the productivity of your plant. You schedule the cleaning to fit your shutdown schedule. The Ondeo Nalco and DDPS team takes it from there.
Jacket space corrosion and deposit control in glass-lined reactors are frequently neglected until fouling problems arise, extending heating and cooling times, compromising product quality, and reducing productivity. Traditional methods of reactor jacket cleaning with acid or alkaline solutions are risky or ineffective. ReStor, a unique, pH-neutral cleaning program has been demonstrated to have the ability to safely restore reactor heat transfer and significantly improve glass-lined reactor efficiency by removing mineral deposits without damaging the glass lining or the reactor base metal.