Highly corrosion resistant, smooth & non-porous.
QVF® Glass components.
Universal glass with optimum quality for all applications.
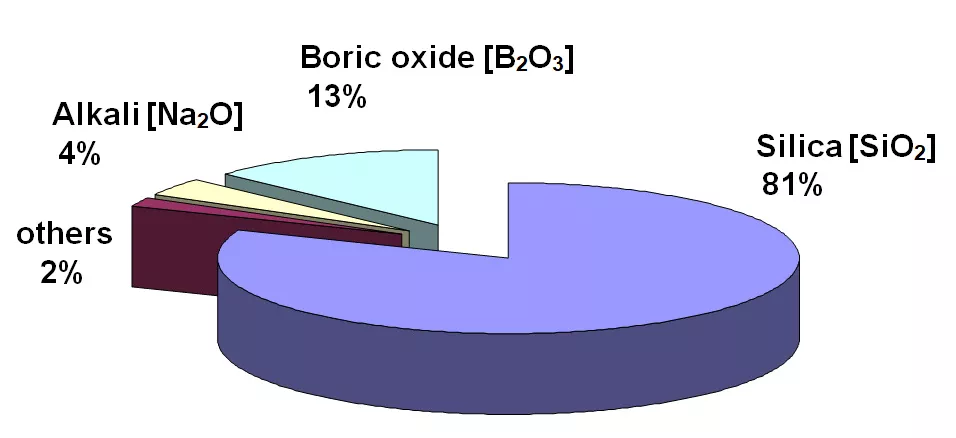
Chemical composition
The special properties – especially its high chemical resistance, its resistance to temperature and its low linear expansion coefficient – of the borosilicate glass 3.3 exclusively used for QVF® glass components for the construction of glass plants and pipelines are achieved by strict adherence to its chemical composition, which is as follows:
Chemical Resistance
A multipurpose glass with optimum quality, for all products
Borosilicate glass 3.3 is resistant to chemical attack by almost any product, which makes its resistance much more comprehensive than that of other well-known materials. It is highly resistant to deionized water, saline solutions, organic substances, halogens such as chlorine and bromine and most acids. There are only a few chemicals which can cause noticeable corrosion of the glass surface namely hydrofluoric acid, concentrated phosphoric acid and strong caustic solutions at elevated temperatures. However, at ambient temperatures caustic solutions up to 30% concentration can be handled by borosilicate glass without difficulty.
Borosilicate glass 3.3 can be classified in accordance with the relevant test methods as follows (see also ISO 3585 and EN 1595):
- Hydrolytic resistance at 98 ºC -Hydrolytic resist. grain class ISO 719-HGB 1
- Hydrolytic resistance at 121ºC - Hydrolytic resist. grain class ISO 720-HGA 1
- Acid resistance - Deposit of Na2O < 100 mg/dm² to ISO 1776
- Alkali resistance - Alkali resistance class ISO 695-A2
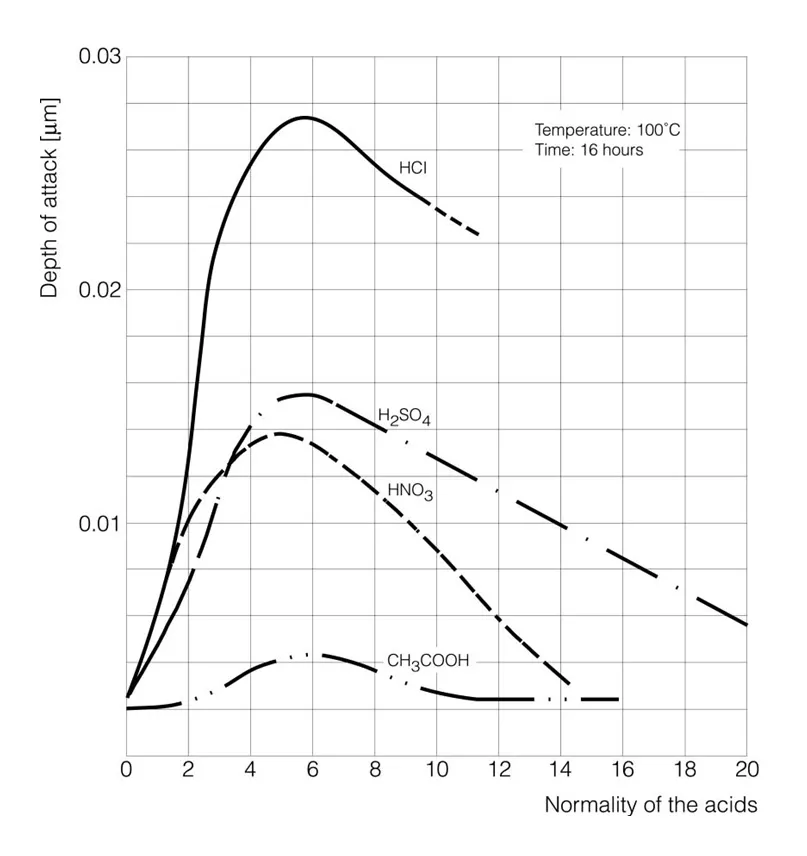
Acid Attack
The corrosion curves show a maximum for different acids in the concentration range between 4 and 7 N (HCl for example at the azeotrope with 20.2 wt %). Above that the reaction speed decreases markedly so that the eroded layer amounts to only a few thousandths of millimeter after some years. There is, therefore, justification for referring to borosilicate glass 3.3 as an acid-resistant material.

Alkaline Attack
It can be seen from the corrosion curves that the attack on the glass surface initially increases as the concentration of the caustic solution increases but after exceeding a maximum it assumes a virtually constant value. Rising temperatures increase the corrosion, while at low temperatures the reaction speed is so low that reduction of the wall thickness is hardly detectable over a number of years.
Physical Properties
Borosilicate glass 3.3 differs from other materials of construction used for process plant not only because of its virtually universal resistance to corrosion (see above) but also because of its very low thermal expansion coefficient. There is, therefore, no need for expensive measures to compensate for thermal expansion resulting from changes in temperature. This becomes of particular significance in the layout of long runs of glass pipeline.
The most important physical properties for the construction of plant are listed below (see also ISO 3585 and EN 1595).
- Linear thermal expansion coefficient - a 20/300 = (3,3 ± 0,1) x 10-6 K-1
- Thermal conductivity between 20 and 200°C - l 20/200 = 1,2 W m-1 K-1
- Specific heat capacity between 20 and 100°C - Cp 20/100 = 0,8 kJ kg-1 K-1
- Specific heat capacity between 20 and 200°C - Cp 20/200 = 0,9 kJ kg-1 K-1
- Density at 20°C - r = 2,23 kg dm-³
Mechanical Properties
The permissible tensile strength of borosilicate glass 3.3 includes a safety factor which takes into account practical experience on the behavior of glass and, in particular, the fact that it is a non-ductile material. Unlike other materials of construction used for similar purposes, it is not able to equalize stresses occurring at local irregularities or flaws, as happens in the case of ductile materials such as metals. The safety factor also takes into account additional processing which components may have undergone (ground sealing surfaces), handling of the glass (minute surface damage) and permissible pressures and temperatures to which it may be subjected in use.
The design figures indicated in the table below and specified in EN 1595 therefore apply to the permissible tensile, bending and compressive stress to which glass components may be subjected taking into account the likely surface condition of the glass in service.
- Tensile and bending strength - K/S = 7 N mm-²
- Compressive strength - K/S = 100 N mm-²
- Modulus of elasticity - E = 64 kN mm-²
- Poisson‘s ratio (transverse contraction figure) - n = 0,2
You have question?
Our teams are ready to collaborate with you and provide solutions for your projects