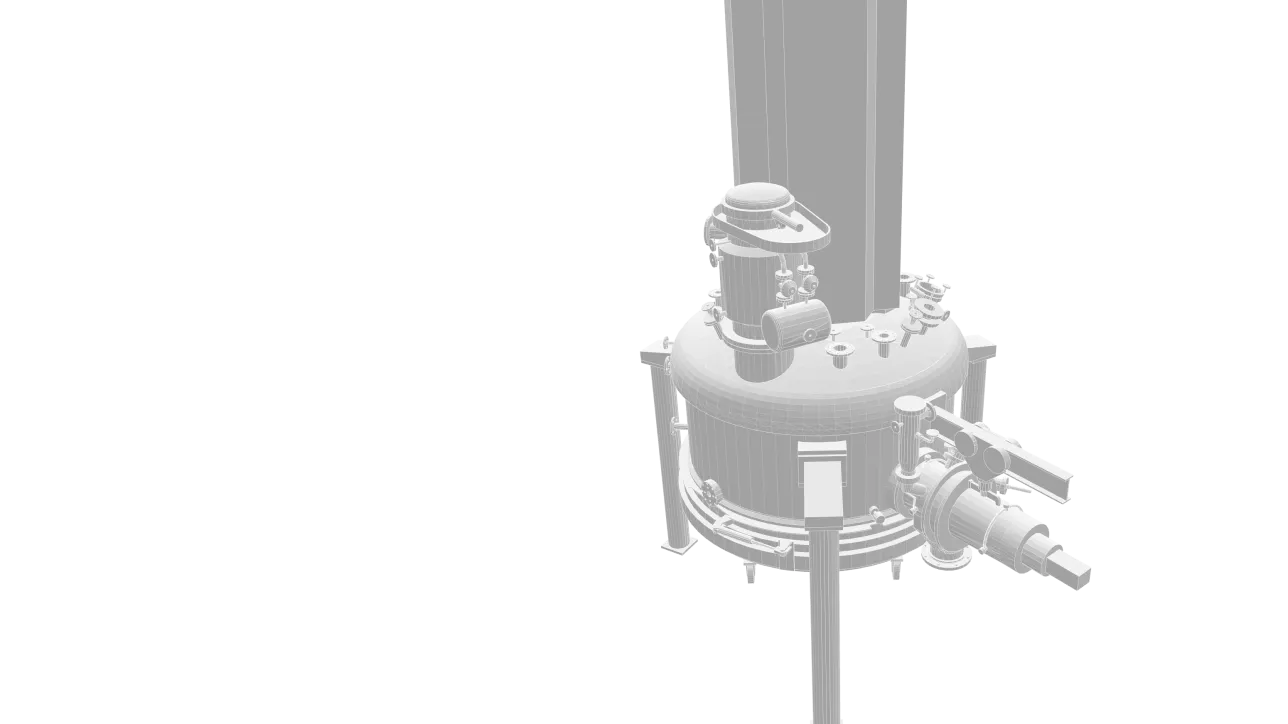
Filtering Bottom Extractor
The essential Filter / Dryer for non-sophisticated operations
Alloy Extraction & ConcentrationThe essential Filter / Dryer for non-sophisticated operations
Alloy Extraction & ConcentrationEnvironmental-friendly extraction of with supercritical CO2
Alloy Extraction & Concentration