Agitators in Nutsche Filter / Dryers
Agitated Nutsche Filter / Dryers have been around for decades and have been designed for industrial applications, particularly in the pharmaceutical and fine chemical industries.
These pressurized filter / dryer designs are in virtually every API (Active Pharmaceutical Ingredient) manufacturing process and are valued for the ability to combine filtration, washing and drying steps of the process in one piece of equipment.
While the agitator is not involved in the actual filtration step, it plays a critical role in the majority of other steps that comprise the nutsche filtration and drying process.
WASHING
Agitators greatly improve the efficiency of the washing process. Re-slurry washing can be performed if additional extraction or dissolution of impurities is necessary. This is executed by the addition of fresh wash liquid that is mixed with the solids.
The agitators feature angled and profiled blades for axial and radial mixing of the solids. While they are robust in design and function, they are also designed to maintain the integrity of a fragile product.
The tip speed is gentle enough to use in applications involving crystals. The blade geometry eliminates the concern for shearing or crystal damage.
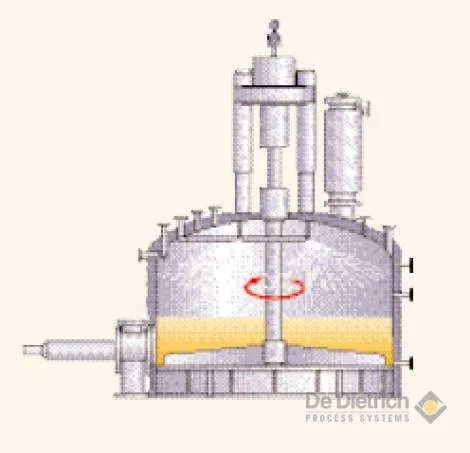
SMOOTHING
Here, the agitator works to smooth out any cracks that may have formed in the product cake. This is especially helpful during displacement washing or nitrogen blow through.
By smoothing and eliminating cracks, the process can avoid bypass or channeling that limits the washing effectiveness.
De Dietrich Process Systems’ filter/dryers utilize a two-blade or three-blade agitator.
These unique designs are built for low speed and high torque service to smooth and compress thick, wet or dry cakes.
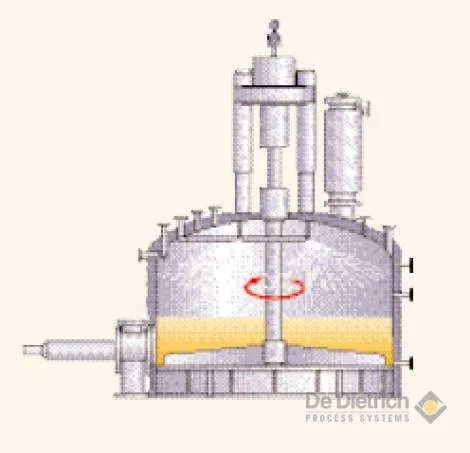
DRYING
Agitators have the option of being heated, which can further decrease drying time by increasing the heat transfer area of the filter/dryer (in addition to the heated filter base and vessel walls).
The heated fluid that runs through the agitator shaft and arms accounts for more than 50% of the heat used for drying. The unique channel designs of the Rosenmund® heated agitator create high velocity flow and increased heat transfer rates. Using a heated agitator in the drying process more than doubles the heat being applied to the solids, which drastically reduces drying time. The drying time can vary, as it is dependent on the product, equipment size, and other factors...
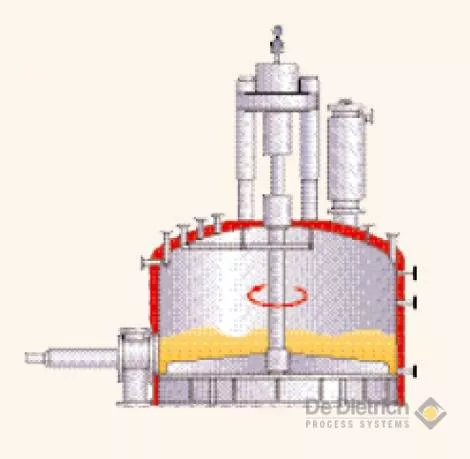
DISCHARGING
There are various ways to discharge product from a filter/dryer, the most common method being through a side discharge valve.
During this procedure, the agitator rotates and “pushes” or offloads the product into a container.
The agitator profile allows for material to naturally flow to the sidewall for material discharge.
In addition, the agitator speed and decent rate can be used to control the speed of discharge during packaging or offloading operations.
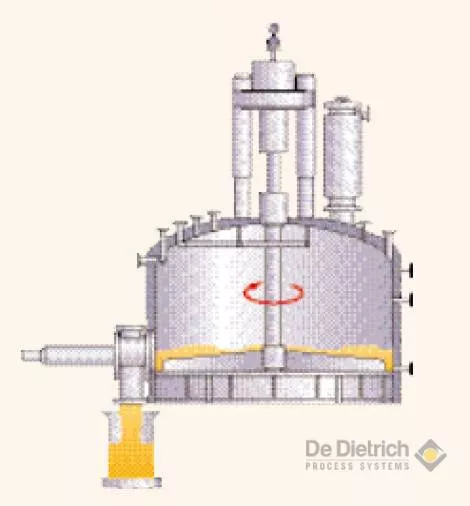
This specially designed, slow speed, robust agitator assembly features “S” type agitator blades that perform different movements designed to carry out specific operations.
The agitator plays a key role in the washing, smoothing, drying and discharging of a Nutsche Filter / Dryer.