Nitric Acid Treatment
Efficient recovery, purification, and concentration of HNO₃
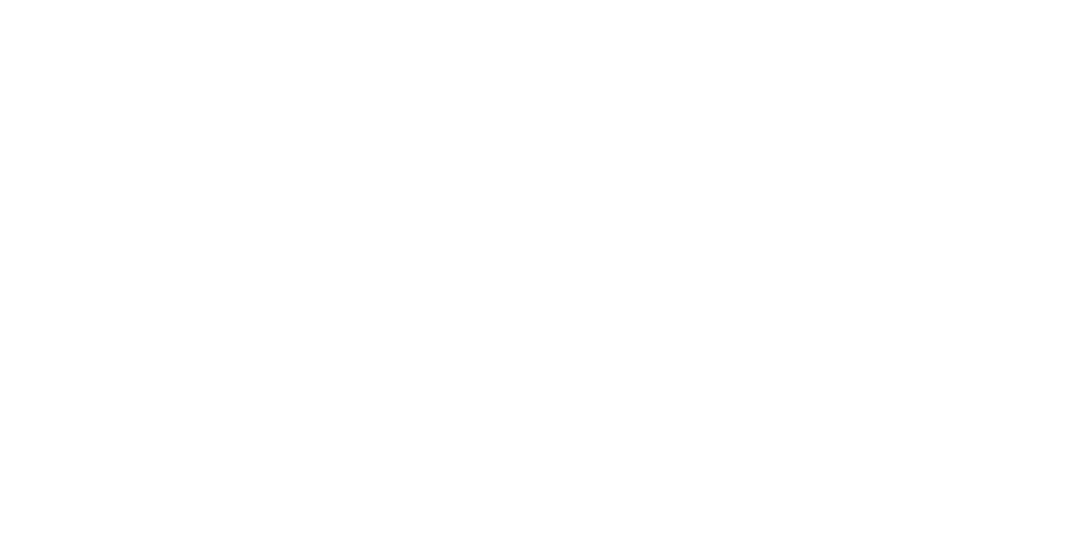
Advanced solutions for nitric acid recovery and reuse
Nitric acid (HNO₃) is essential in fertilizer production, chemical synthesis, and industrial processes, yet its waste streams pose environmental and economic challenges. De Dietrich provides state-of-the-art technologies for the recovery, purification, and concentration of nitric acid, ensuring cost savings, sustainability, and regulatory compliance. Our systems allow for the recycling of nitric acid from spent solutions, gas streams, and mixed acid waste, significantly reducing industrial waste and raw material consumption.
Performance & Safety
High-purity nitric acid recovery – Eliminates impurities for industrial reuse
Corrosion-resistant materials – Designed for aggressive acid environments
Energy-efficient acid concentration – Optimized for cost-effective operation
Scalable systems – Adapted for pilot trials to large-scale production
Innovative technologies for HNO₃ purification
Our custom-engineered nitric acid recovery solutions enable industries to reduce waste, lower costs, and improve process efficiency. Using borosilicate glass and glass-lined steel, our systems ensure maximum durability and safety, even under extreme chemical conditions. Whether for denitration, purification, or recycling, De Dietrich delivers solutions that align with your sustainability and performance goals.
Key Applications
Recovery of nitric acid in fertilizer and explosives production to improve efficiency
Denitration of waste streams in chemical and industrial processes
Purification of nitric acid for electronic and pharmaceutical-grade applications
Recycling of mixed acid waste for cost-effective resource management
Customized systems for high-efficiency acid recovery
De Dietrich offers comprehensive solutions, from pilot-scale testing to full industrial implementation, ensuring that your nitric acid treatment process is optimized for yield, safety, and compliance. Our extensive process knowledge and innovative engineering help industries meet sustainability targets while maximizing operational efficiency.
Looking for a safe and efficient nitric acid treatment solution?
Documents to download
Request a download
In order to process your brochure request efficiently, we kindly ask you to provide the required information through our form.