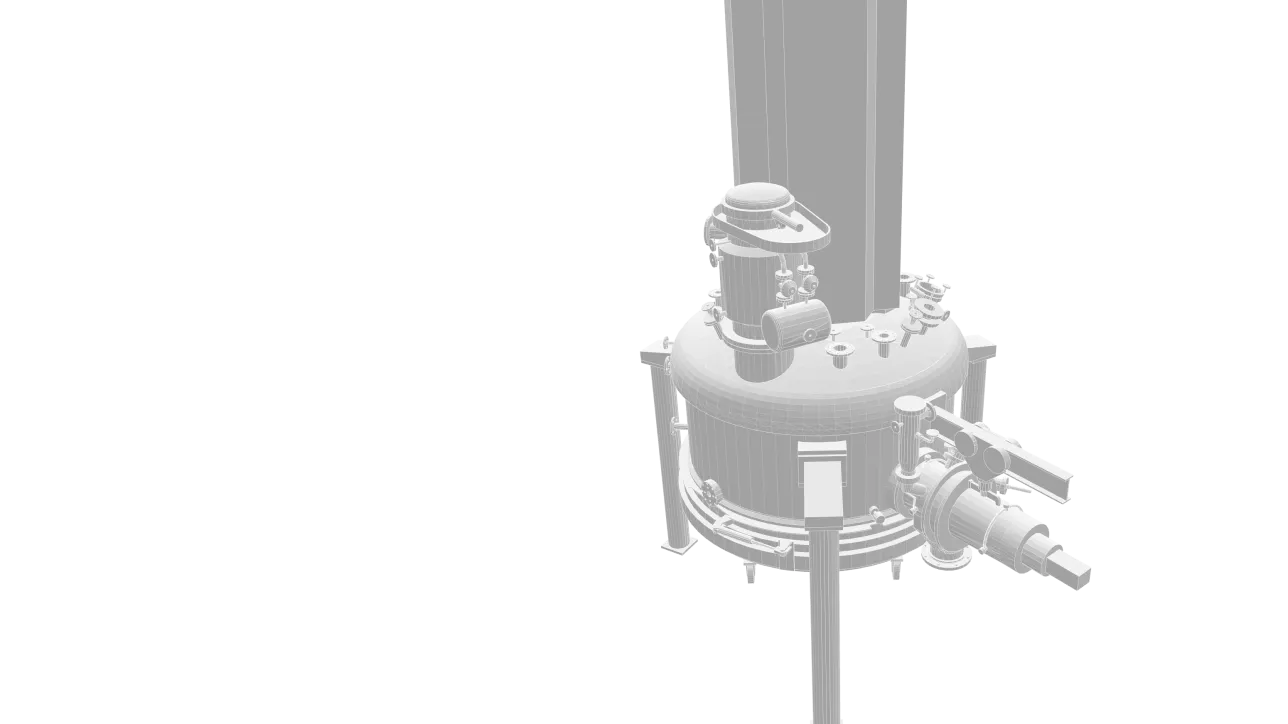
Extractor de fondo filtrante
Este diseño actualizado se centra en las funciones clave de los Filtros / Secadores con soluciones seleccionadas que preservan las operaciones críticas a su nivel óptimo.
Aleación Extracción y concentraciónEste diseño actualizado se centra en las funciones clave de los Filtros / Secadores con soluciones seleccionadas que preservan las operaciones críticas a su nivel óptimo.
Aleación Extracción y concentraciónEquipo completo de extracción multietapa listo para el uso
Vidrio Extracción y concentraciónExtracción supercrítica de sólidos y de líquidos (SCFE).
Aleación Extracción y concentración