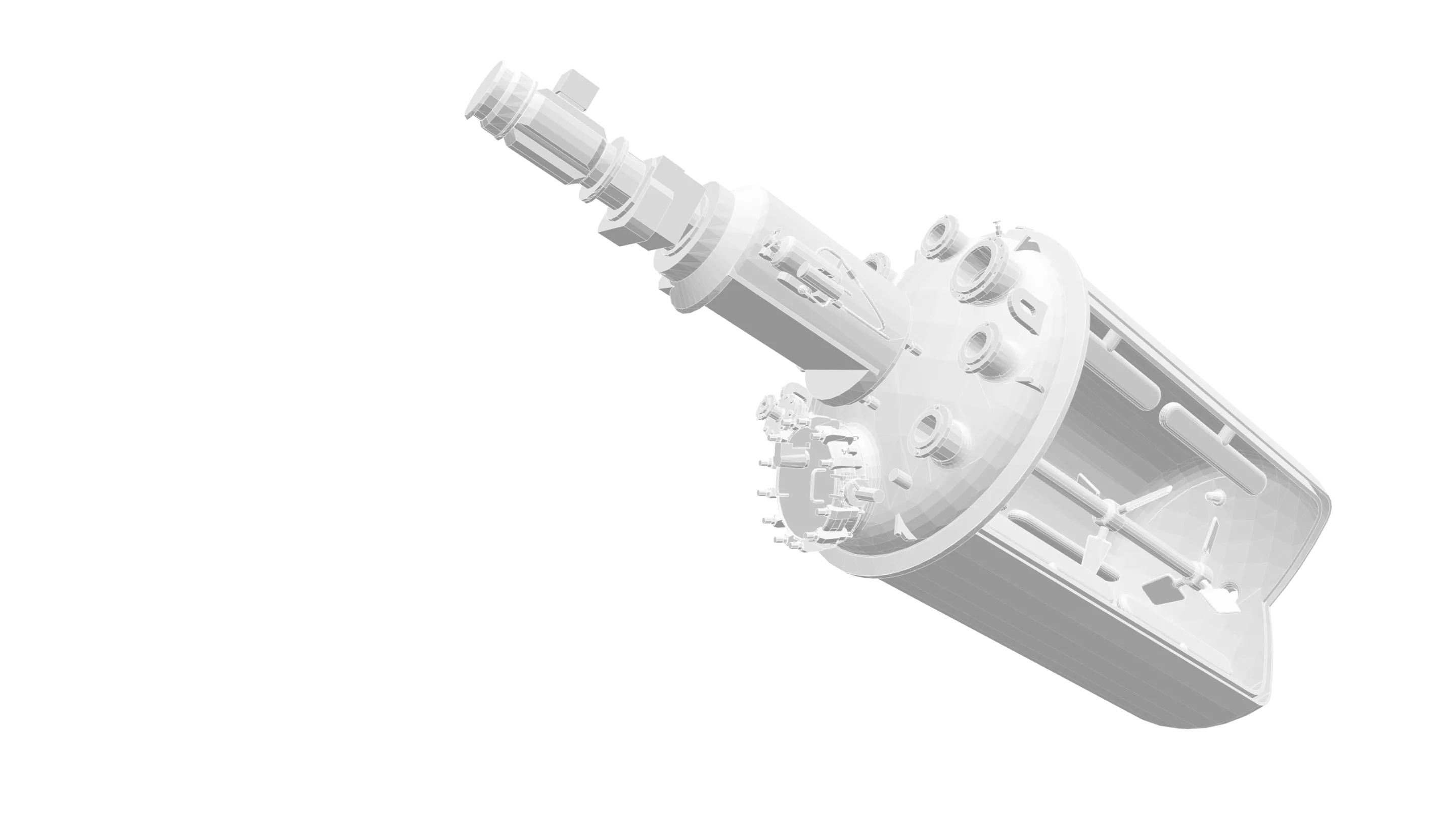
The OptiMix®
Exclusively from De Dietrich, the OptiMix® reactor design offers tremendous optimization of the mixing performance by integrating three baffles on the vessel wall and a temperature probe in the bottom part of the vessel. The OptiMix® design can be applied to all reactors in the DIN range (AE, BE, CE)
OptiMix® reactor: The efficient technology
This patented design enhances heat transfer, solids suspension and distribution, gas dispersion, gas flow rates and mass transfer.
The OptiMix glass-lined reactor's performances are based on the integration of three baffles onto the vessel wall. This leads to a notable improvement in terms of mixing and heat transfer effeciency compared to standard reactors.
This specific design also frees up nozzles that can be used for your process or for the installation of options such as sampling devices, spray balls and much more.
The profile of the blades prevents the accumulation of crystals in the event of crystallization. This design satisfies two of industry's primary requirements: optimal process efficiency and improved cleanability of the reactor, as well as a reduction of the amount of dead zones which generally occurs with a standard, nozzle-mounted baffle.
Optimix is also available in an Optimix HE version (heat exchange), which improves heat exchange even further.
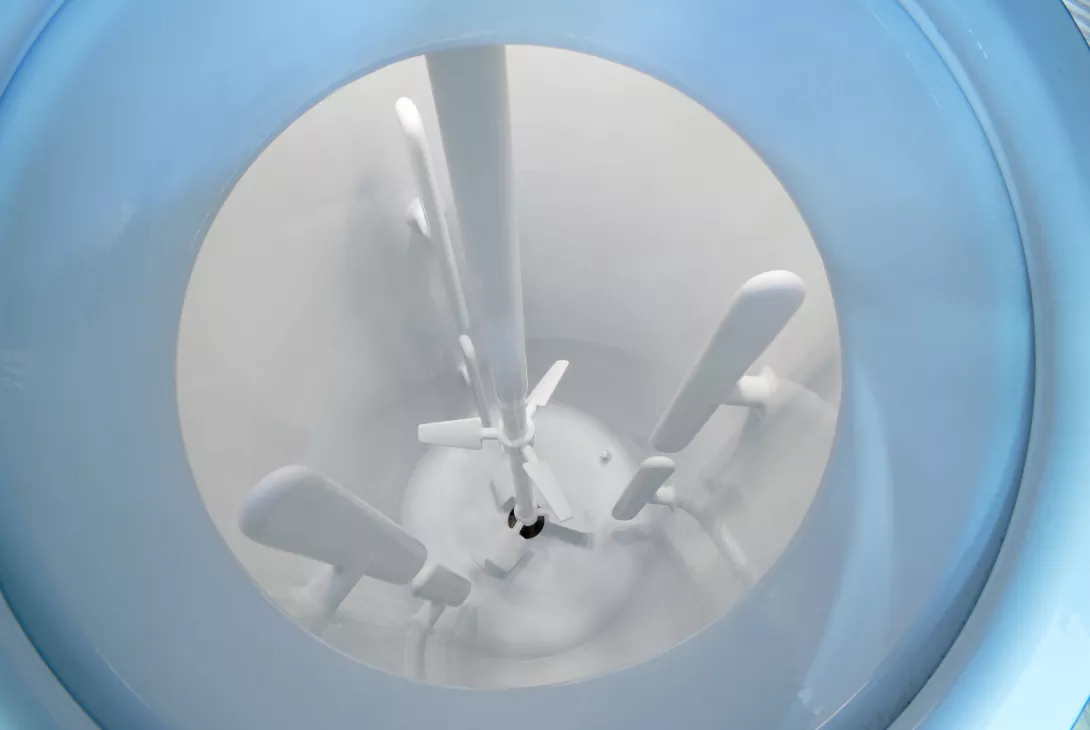
The polyvalence and reliability in every circumstances
OptiMix reactors are lined with DD3009 glass for superior corrosion resistance and easy cleaning.
They are also fitted with an integrated temperatur sensor in the bottom part which enables control of very small reaction volumes.
Components are interchangeable with standard reactors of the same size. OptiMix reactors can be equipped with jacket or half coil and are usually proposed with a GlasLock® agitator to improve mixing performances even further.
OptiMix benefits
Heat and mass transfer improvement
Easy to clean, no dead zone, no splashing, no floating products.
Baffles are distant from the wall : no deposits on walls, no expansion stresses on baffles, no heating / cooling slope limitation
No more vortex & less waste
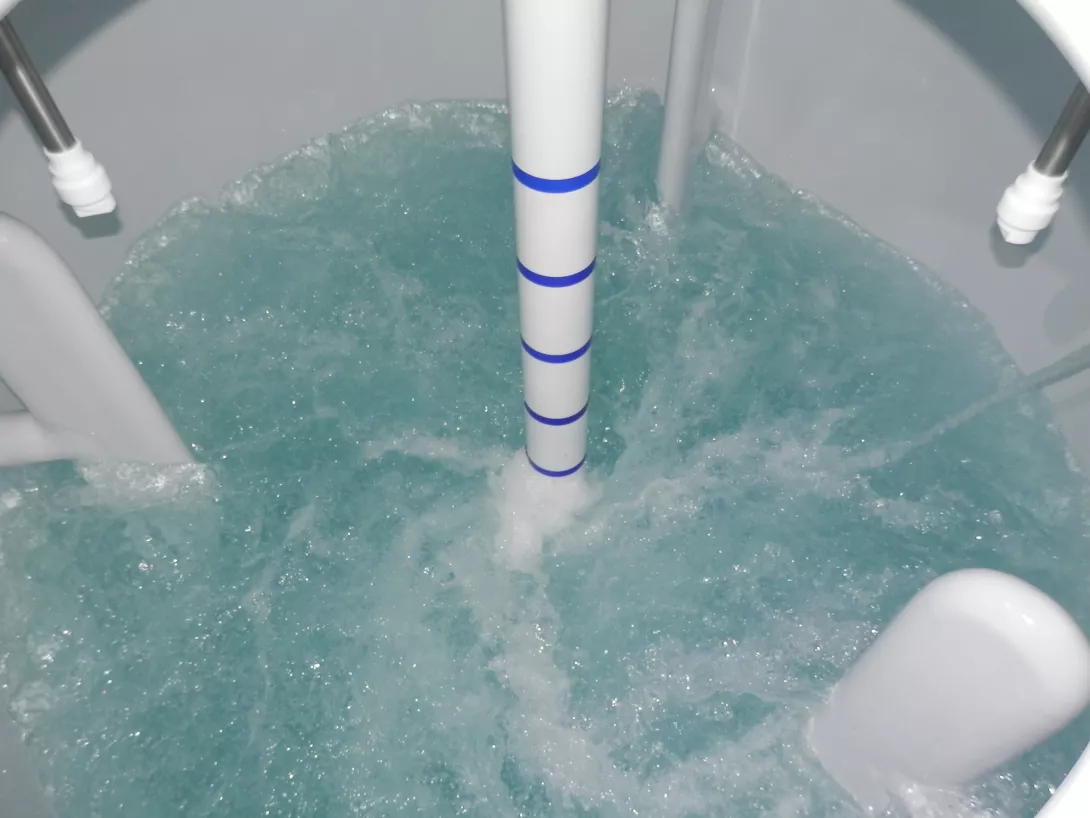
OptiMix® - HE (Heat Exchange)
Increase your heat exchange surface with the new generation of OptiMix - HE reactors
This new design uses the thermal fluid contained in the half-coil in order to create a circulation through the baffles.
As a result, film coefficients and heat transfer rates are higher than in conventional jackets.
By combining the advantages of the OptiMix’s three integrated wall baffles, we can now offer a high performance glass-lined reactor.
This results in an increased heat transfer performance up to 25%
You have questions?
Our teams are ready to collaborate with you and provide solutions for your projects
Documents to download
Request a download
In order to process your brochure request efficiently, we kindly ask you to provide the required information through our form.