Rotary Evaporator
QVF® ROTADEST solution for solvent evaporation, crystallization, drying of suspensions, powders or granulates, various chemical reactions in the liquid phase or Ex-rated areas
Special benefits of the QVF® ROTADEST
- Low vacuum due to high performance mechanical PTFE/ceramic-seal and certified glass flange system
- Mechanical PTFE-seal for slight overpressure or low vacuum
- Exclusive use of corrosion resistant materials as borosilicate glass 3.3 and PTFE for all components being in contact with the product
- FDA-Materials certificates for surfaces in contact with product
- Robust drive unit for the rotary sphere
- Condensation section suited to the process
- Proper observability of the processes
- Reliable and sustainable industrial construction
- Simple operation
- Ex-Protected version available
ROTADEST HIGHLIGHTS
Special benefits of the QVF® ROTADEST
Robust drive unit for the rotary sphere. Condensation section suited to the process, proper observability of the processes. Ex-Protected version available
Low vacuum due to high performance mechanical PTFE-seal and certified glass flange system. Mechanical PTFE/Ceramic-seal for low vacuum
Exclusive use of corrosion resistant materials as borosilicate glass 3.3, PTFE and ceramic for all components being in contact with the product. Materials certificates for surfaces in contact with product
Robust drive unit for the rotary sphere. Reliable and sustainable industrial construction. Simple operation
ROTARY EVAPORATOR
QVF® ROTADEST solution for solvent evaporation, crystallization, drying of suspensions, powders or granulates, various chemical reactions in the liquid phase or Ex-rated areas
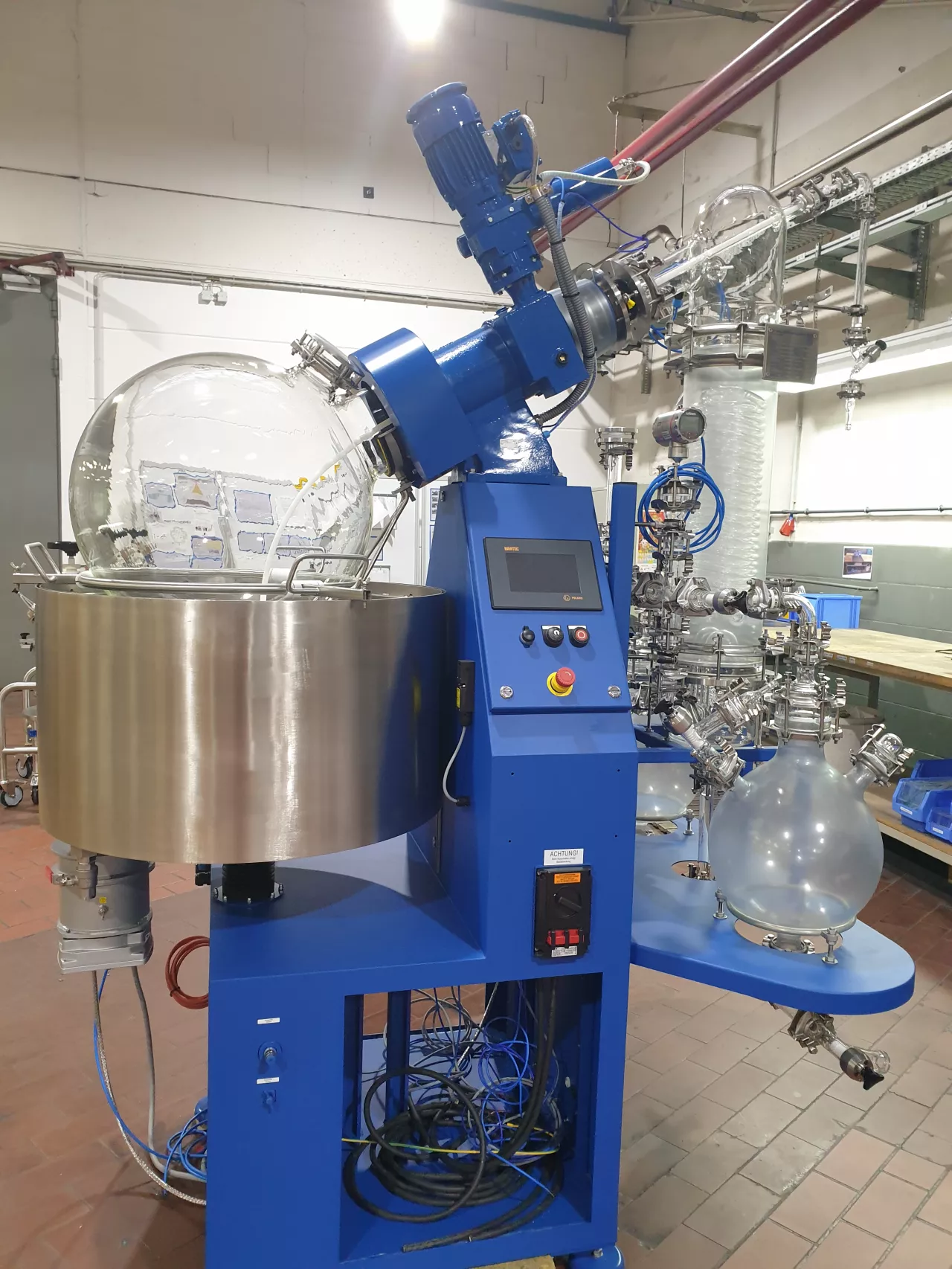
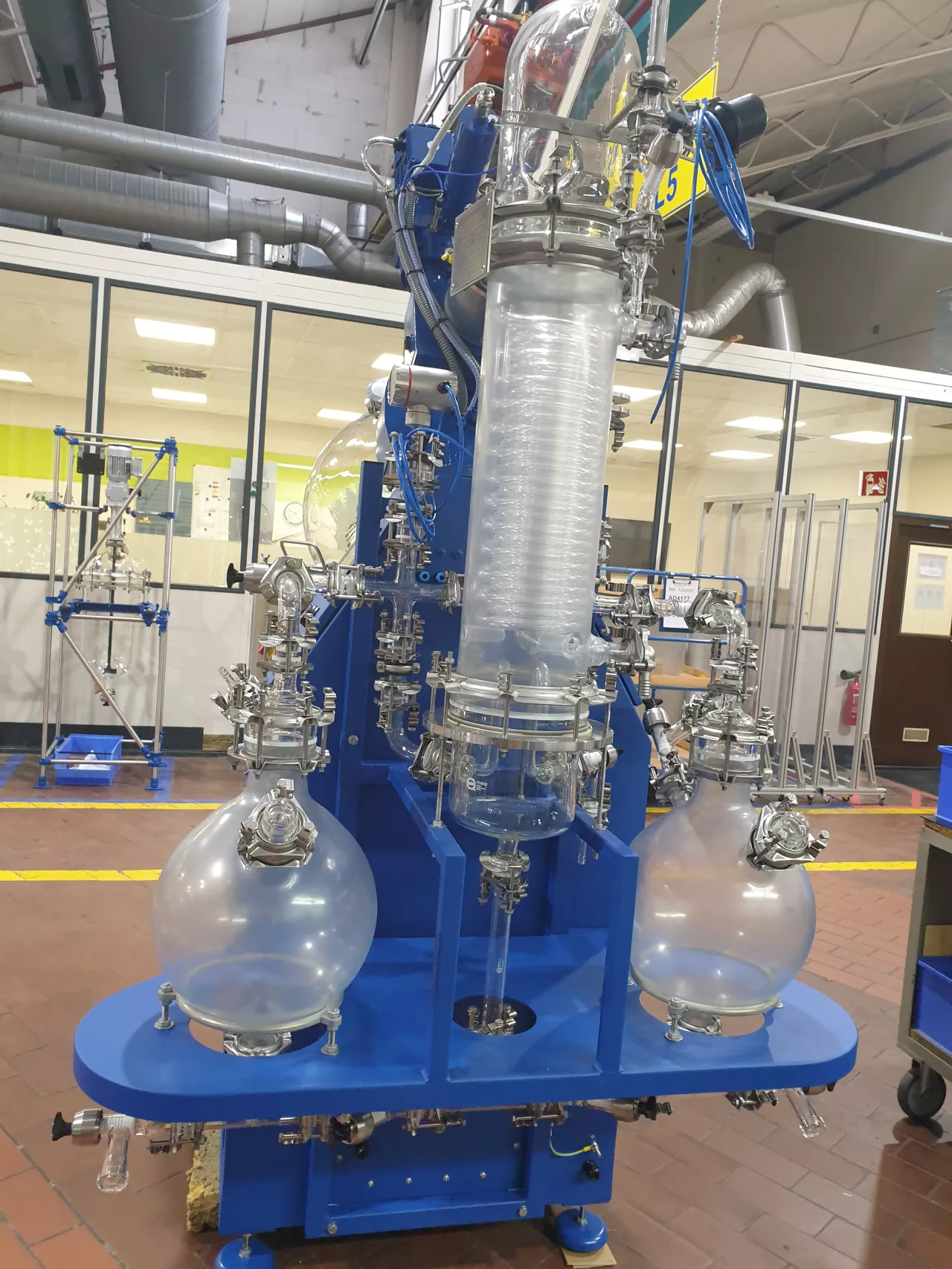
The QVF Rotadest highlights
The most universal solution for gentle and efficient evaporation
Rotary evaporators are mainly used to evaporate light boiling components under normal pressure or vacuum. When used in pilot plant and small scale production they are also suitable for semi-continuous evaporation. They are characterized by providing a gentle thermal treatment for temperature-sensitive mediums and provide a higher evaporation rate as non-stirred glass distillation flasks. Compared to other evaporation processes the unique process feature of rotary evaporators is their ability to evaporate all volatile media providing at the end a dry product in the flask.
The process conditions are limited by the maximum temperature of the heating bath ( max. ~ 160°C) , the temperature of the cooling liquid (e.g. ~ 15°C tap water) for the condenser and the vacuum generator ( e.g.~10mbar).
The QVF® ROTADEST can be supplied for EX-rated areas up to zone 1 IIB.
The liquid to be processed in the rotary evaporator is either charged batch wise by gravity, by a pump or sucked-in by vacuum into the evaporation flask.
The liquid to be processed in the rotary evaporator is either charged batch wise by gravity, by a pump or sucked-in by vacuum into the evaporation flask. During the evaporation process further feed can be added by means of a pump, gravity or by the operating vacuum through the PTFE-hose passing the rotating shaft and ending in the spherical vessel. The rotating sphere is half way rotating through the liquid in a heating bath filled with water or another suitable liquid heating fluid. The bath is heated by means of electrical heating elements and can be lowered to immediately stop the evaporation process.
The rotation of the sphere which is flanged to the geared motor ensures an effective mixing of the product inside the vessel and wets the complete inner surface of the sphere, increasing the evaporation surface, therefore increasing the evaporation rate and hence shortening the evaporation time.
The components with the lower boiling point are evaporated in the rotating sphere first.Their vapours flow through a sleeve shaft integrated in the drive and enter the condenser assembly. The vapours are condensed and optionally cooled in an distillate cooler before being captured in a final distillate receiver.
- Most universal type of evaporator
- Gentle evaporation due to film evaporation
- Evaporation down to the dry product
- Reducing foam generation due to reduced bubbling
- Avoiding hazardous bumping boiling
- Reliable industrial design
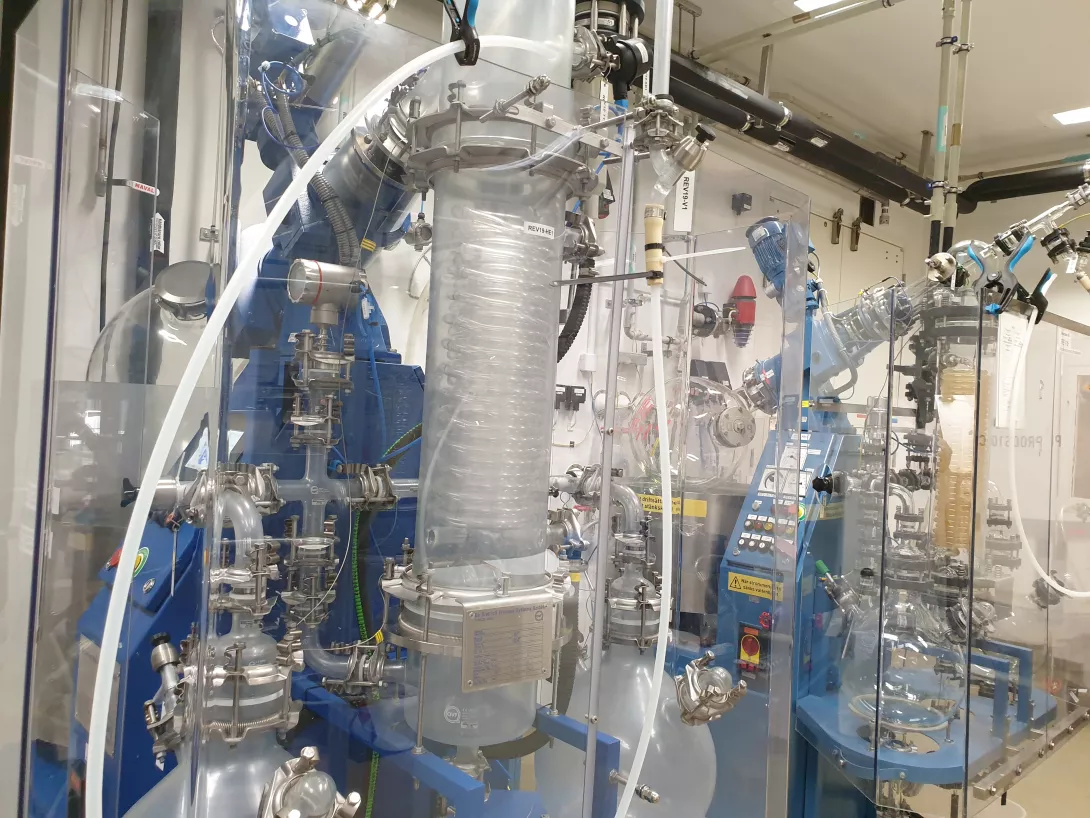
You have questions?
Documents to download
Request a download
In order to process your brochure request efficiently, we kindly ask you to provide the required information through our form.