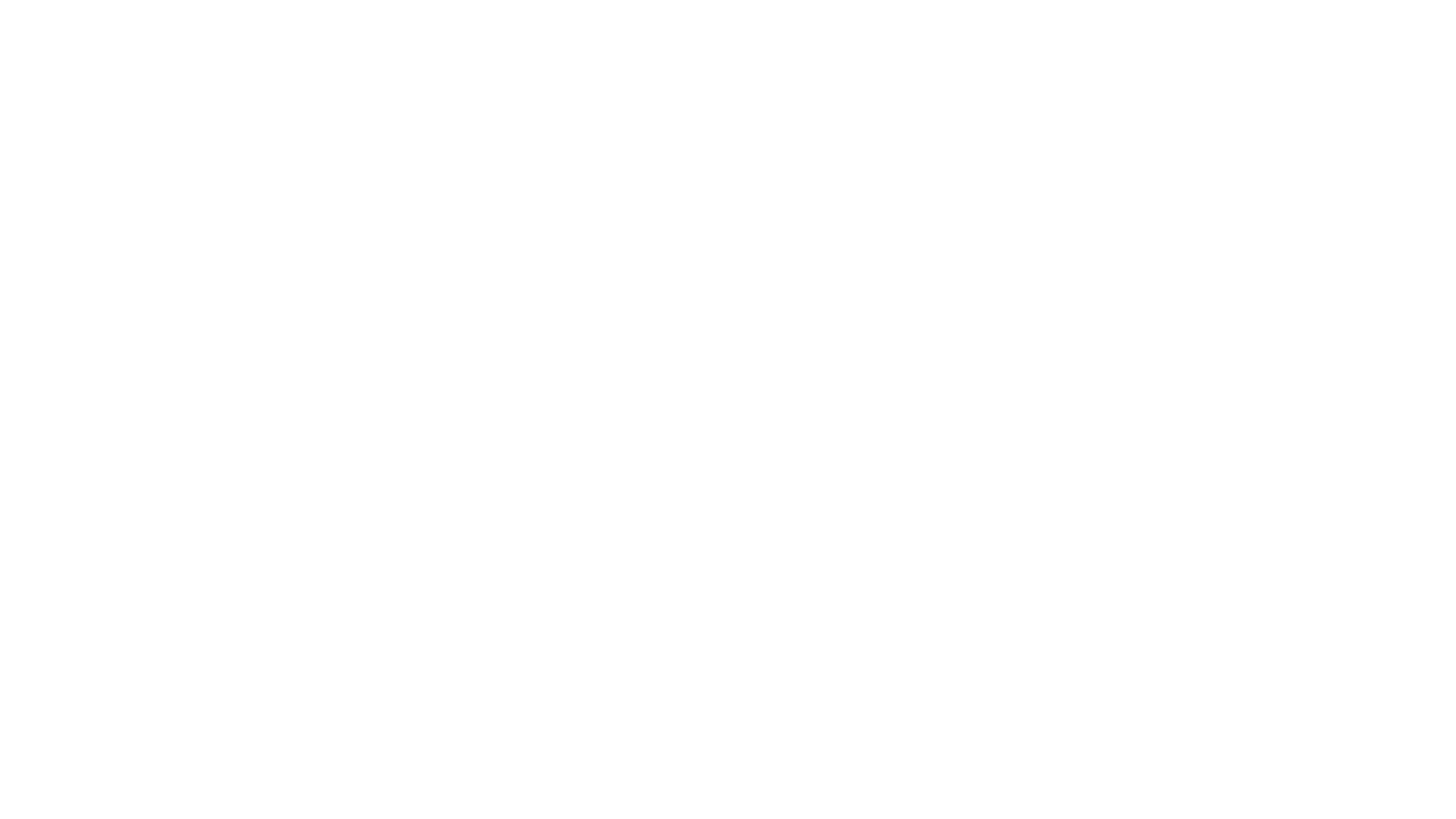
Recuperación de ácido acético
La recuperación de ácido acético de corrientes acuosas maximiza su eliminación, recupera subproductos orgánicos y minimiza tanto el contenido de compuestos orgánicos en las aguas residuales como el consumo de energía.
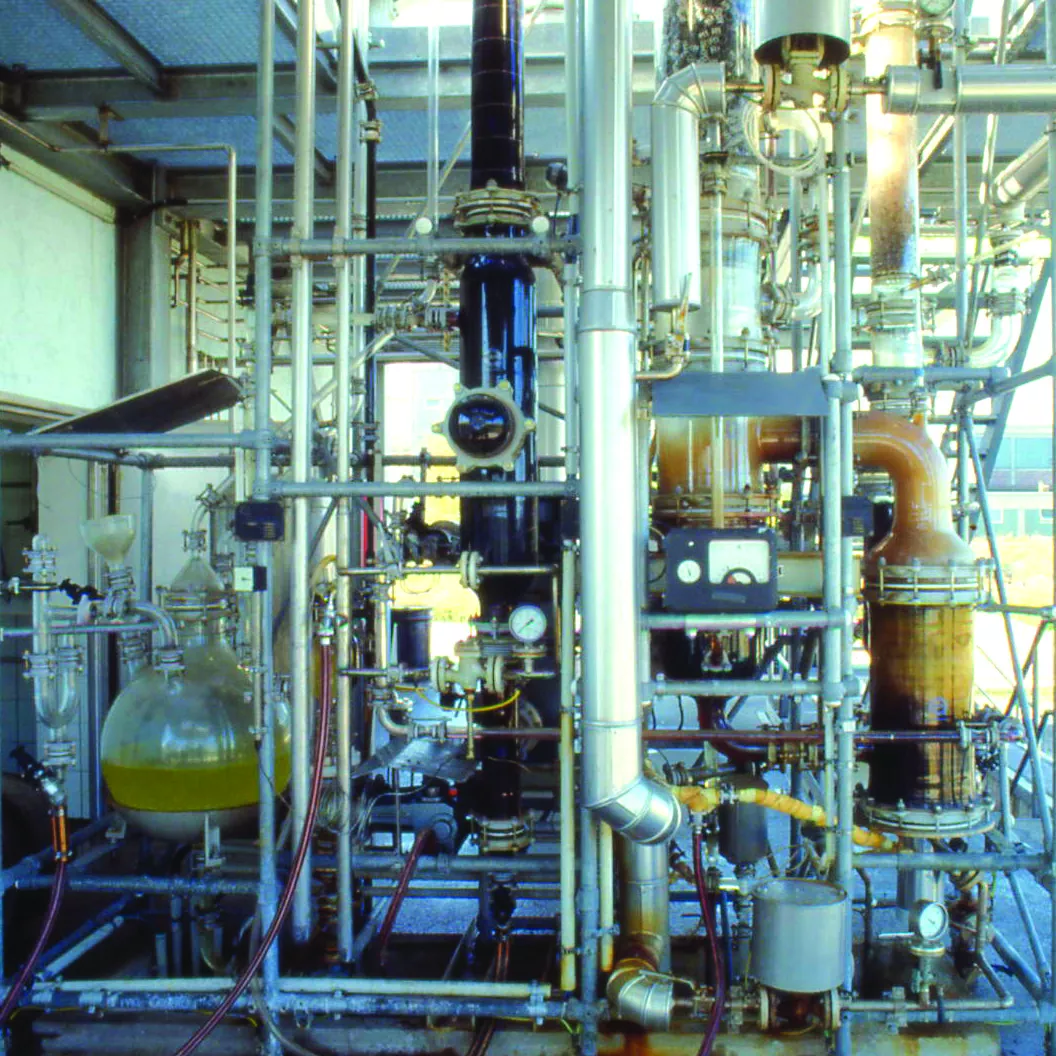
El ácido acético es el ácido carbónico alifático más utilizado, empleado como reactivo, disolvente y en la producción de productos farmacéuticos. Su recuperación es económicamente significativa, pero la separación de la mezcla de ácido acético y agua por rectificación resulta costosa debido a su bajo factor de separación térmica, lo que implica altos costos de energía y operación. Por ello, se emplea la rectificación azeotrópica, con o sin etapa de extracción, según la concentración de ácido acético. La adición de una sustancia auxiliar aumenta la volatilidad del agua, permitiendo la separación con menor consumo energético. En concentraciones de ácido acético inferiores al 40%, se extrae primero con un agente adecuado antes de proceder a la recuperación pura mediante rectificación azeotrópica.
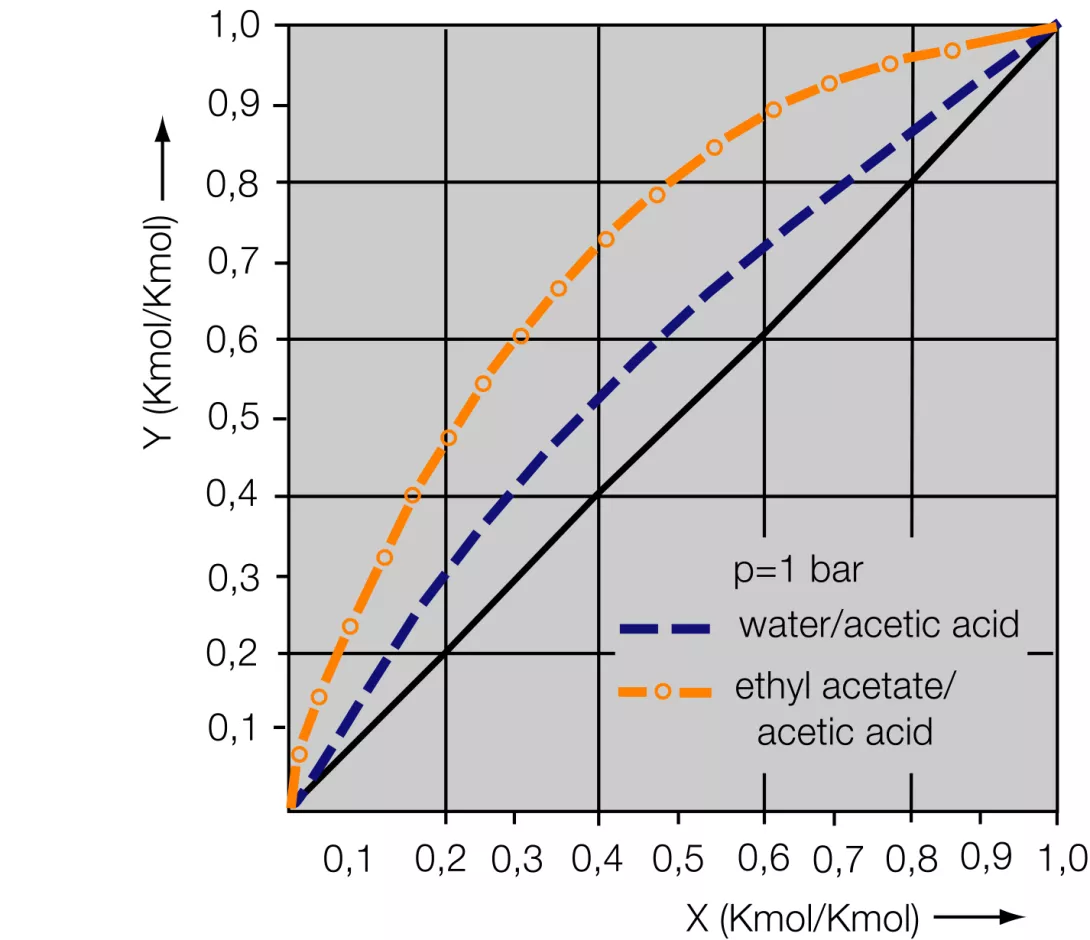
El método de recuperación mediante extracción debe ser considerado, independientemente de la concentración, si las impurezas adicionales en la mezcla inicial, como sales, podrían causar problemas durante la recuperación directa por destilación. Este folleto técnico trata sobre la recuperación de ácido acético mediante extracción líquido-líquido y rectificación azeotrópica posterior.
Selección del agente de extracción
Se utilizan agentes de extracción de bajo punto de ebullición, considerando solubilidad, capacidad de absorción, precio, disponibilidad y requisitos ambientales. La elección del agente depende de la eficiencia energética y el coste de la rectificación del disolvente. Los agentes como EtAc y MTBE son los más eficientes en términos energéticos, aunque su efectividad depende de la concentración de ácido acético (hasta 15% en peso). A mayores concentraciones, es necesario aumentar la cantidad de agente de extracción, lo que incrementa los costos operativos. El método QVF® es más eficiente energéticamente, incluso con altas concentraciones de ácido acético. Para EtAc, la solubilidad con agua limita las concentraciones de alimentación a un 30%, mientras que con MTBE se pueden manejar hasta un 40%.
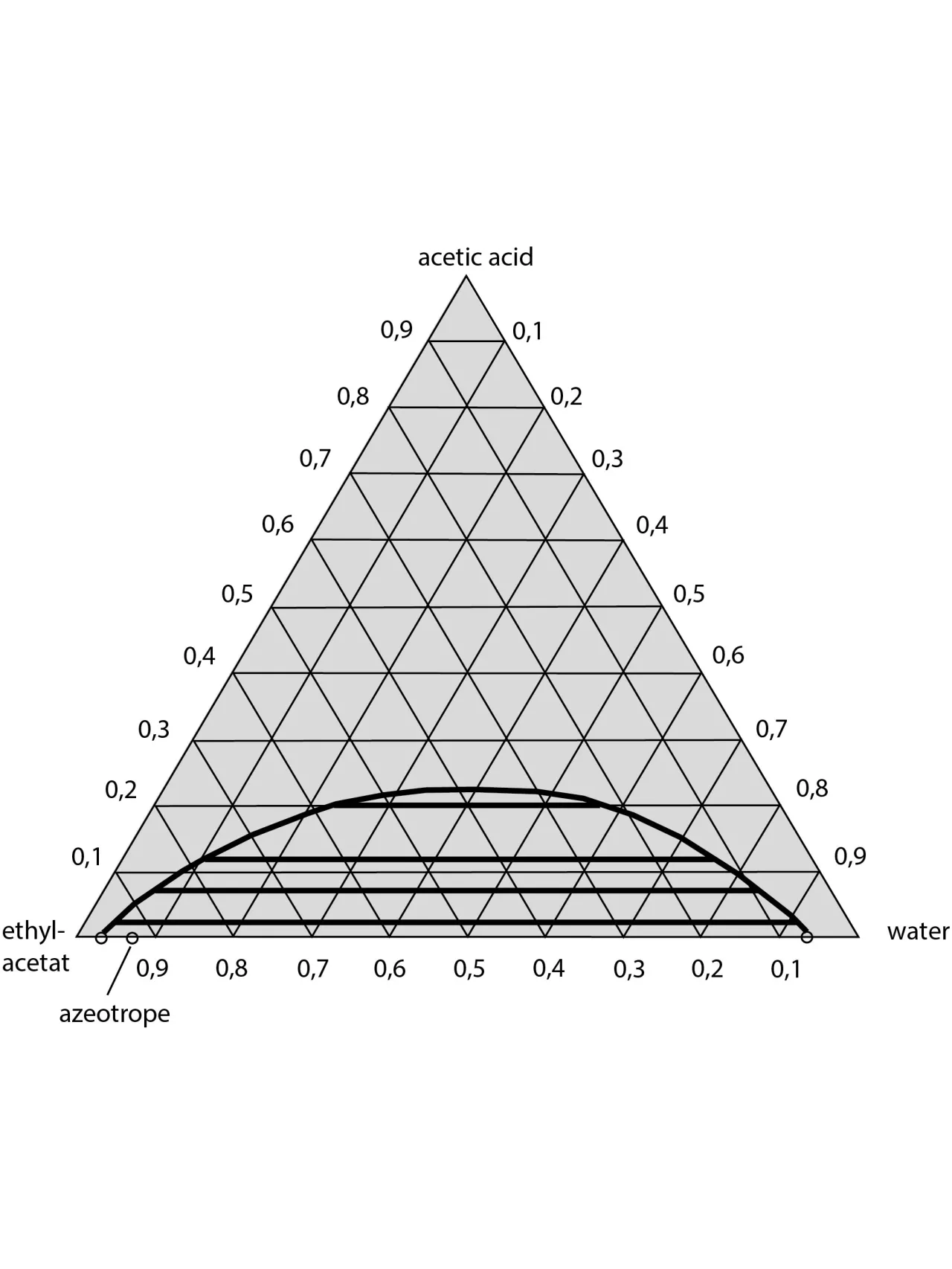
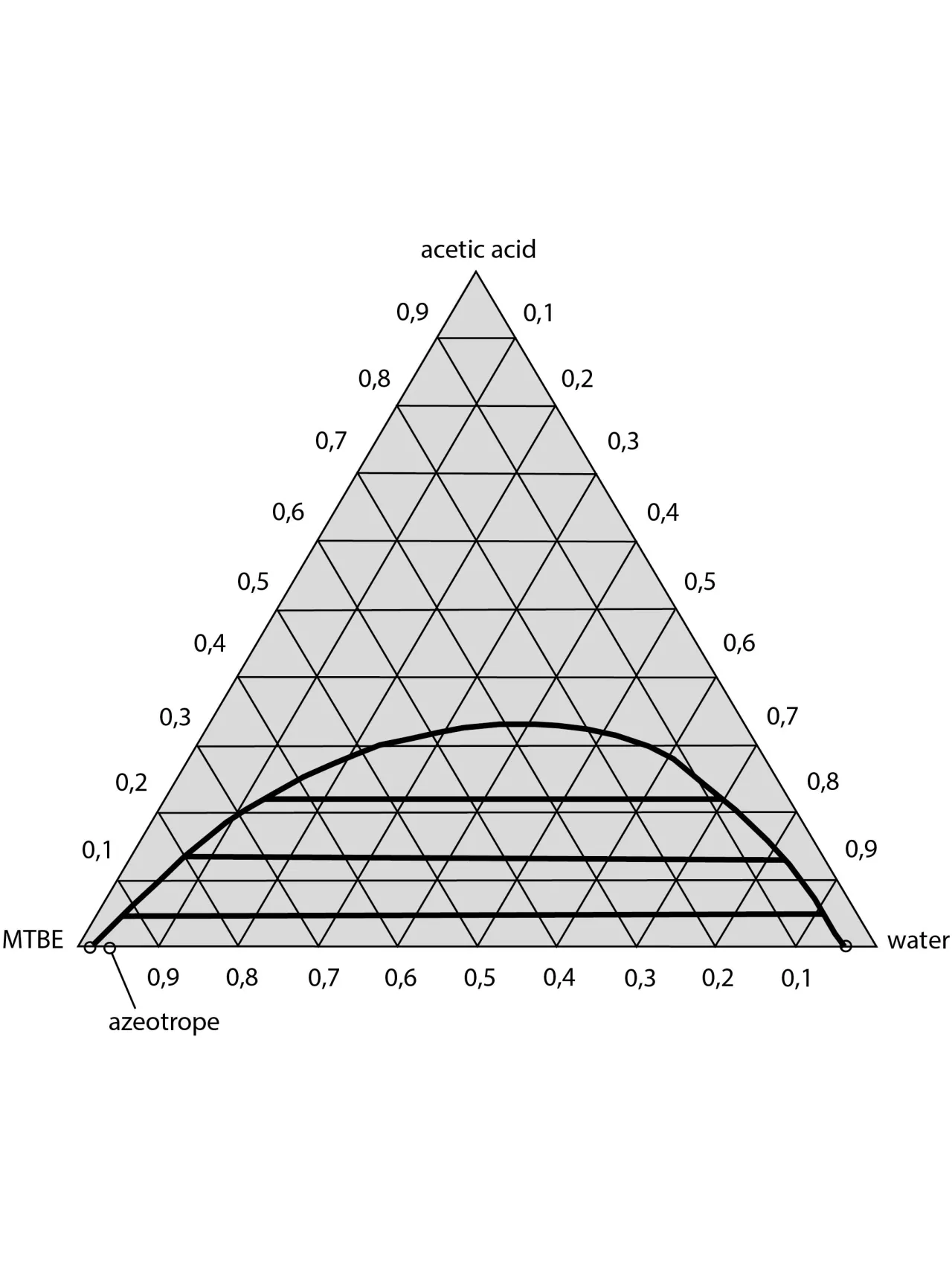
Nombre | Coeficiente de distribución promedio | Densidad | Entalpía de vaporización | Punto de ebullición | Azeótropo |
kg/kg | kg/m³ | kJ/kg | °C | Water T Wt % °C | |
Ethyl acetate C4H8O2 | 0,84 | 900 | 395 | 76,7 | 8,47 70,4 |
Isopropyl acetate, C5H10O2 | 0,55 | 877 | 361 | 88,6 | 10,50 76,5 |
n-Propyl acetate, C5H10O2 | 0,50 | 891 | 336 | 101,6 | 13,20 82,2 |
Methylpropyl ketone, 2-pentanon, C5H10O | 0,97 | 810 | 384 | 102,3 | 19,50 83,3 |
Methylisobutylketon, 4 Methyl- 2-Pentanon C6H12O | 0,50 | 810 | 488 | 115,9 | 24,30 87,9 |
Methyl-tert.-butyl ether, C5H12O | 0,75 | 740 | 322 | 55 | 4 52,6 |
Proceso de extracción
El ácido acético se extrae de las corrientes acuosas mediante una torre de extracción, seguida de una torre de rectificación para recuperar el agente de extracción y una torre de despojo de agua. El proceso convencional usa agentes como el acetato de etilo o MTBE, logrando concentraciones residuales de ácido acético de 0.1-0.5%. El método QVF® optimiza la concentración de ácido acético y la pureza del raffinate, con un control preciso de la fase extraída y el agua en la rectificación.
Los costos están determinados por la separación del agente de extracción, siendo más costoso en el proceso QVF® debido a la necesidad de controlar el perfil de concentración y la relación de reflujo. El sistema de control automático de De Dietrich ha demostrado ser altamente eficiente en la práctica.
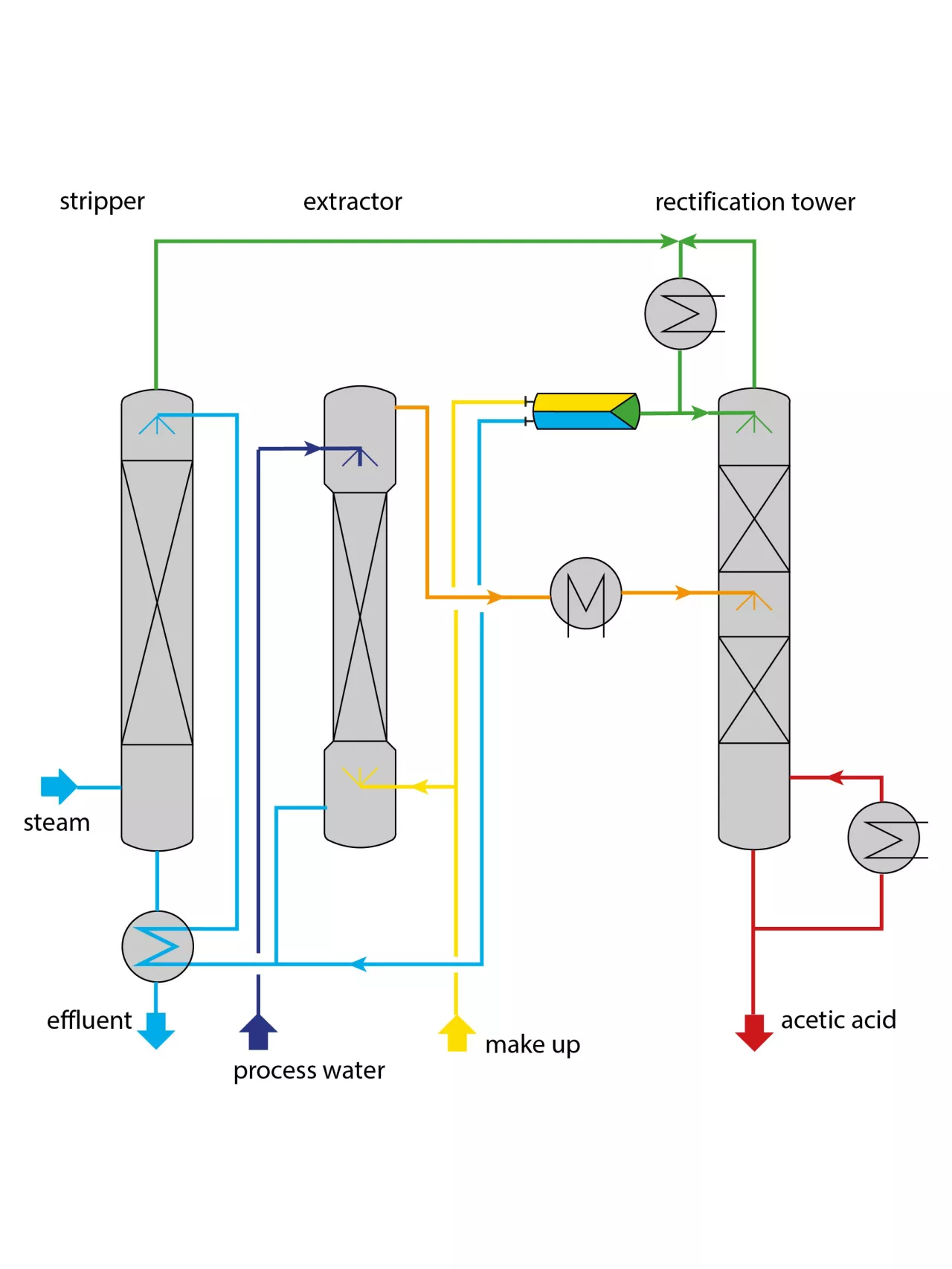
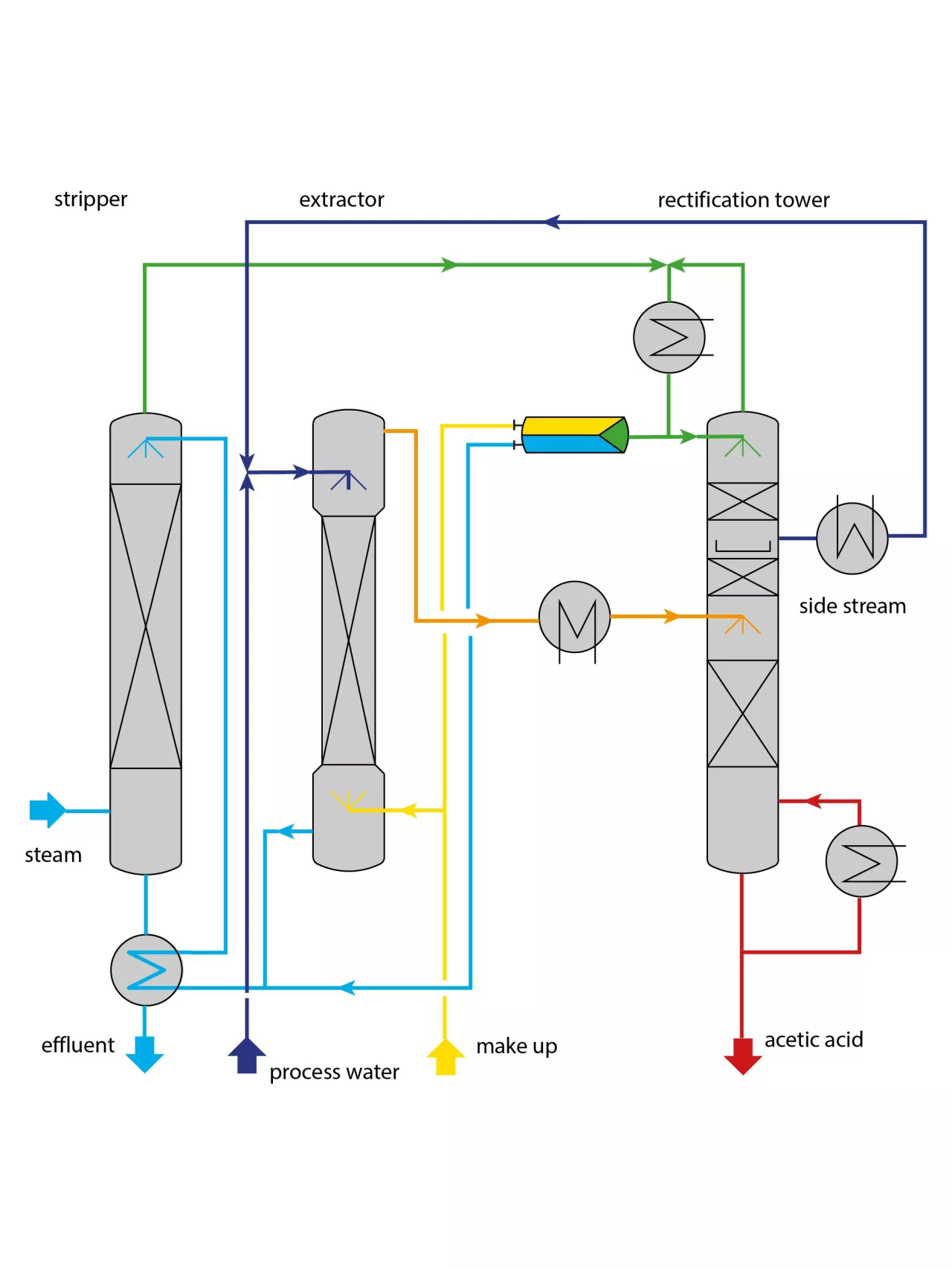
Costes operativos
El proceso QVF reduce los costes operativos gracias a un 40% menos de demanda energética en comparación con el método tradicional. Esto se logra mediante un menor flujo de agente de extracción, que genera altas concentraciones de ácido acético y mayor proporción de agua en el extracto. El exceso de agua se evacua de la columna de rectificación, permitiendo una composición azeotrópica en el destilado.
Los costes dependen de la concentración de entrada y salida del ácido acético, el tipo de agente de extracción y el método de recuperación. A modo de referencia, con MTBE, el proceso clásico requiere aproximadamente 280 kW para 100 kg/h de ácido acético a una concentración de 10%, y 260 kW a 35%. En el proceso QVF, estos valores son 260 kW a 10% y 180 kW a 35%.
Evacuación de componentes secundarios
Cuando el agua de proceso contiene componentes con menor punto de ebullición, como etanol o acetona, estos deben ser eliminados junto con el ácido acético. Con MTBE, los componentes pasan por la columna de extracción sin ser extraídos y se separan en una columna de desorción. Si hay una pequeña diferencia en el punto de ebullición, como con la acetona, puede haber pérdidas de MTBE, y en este caso, se utiliza una columna de desorción sin sección de enriquecimiento.
Eliminación de componentes acompañantes
El agua de proceso puede contener componentes volátiles como etanol o acetona, que deben ser eliminados junto con el ácido acético. Con MTBE como agente de extracción, los componentes volátiles pasan por la torre de extracción sin ser extraídos y se dirigen a una columna de desorción con sección de rectificación. En la sección de desorción, se elimina el agente de extracción y los componentes acompañantes. La sección de rectificación separa el MTBE de estos componentes. Si la diferencia de ebullición entre el MTBE y los componentes es pequeña, como con la acetona, puede haber pérdidas de MTBE. En este caso, se utiliza una columna de desorción sin sección de rectificación, donde los componentes acompañantes se dirigen hacia la parte inferior y el agente de extracción hacia la parte superior. La fase acuosa cargada debe ser purificada, por ejemplo, mediante tratamiento biológico.
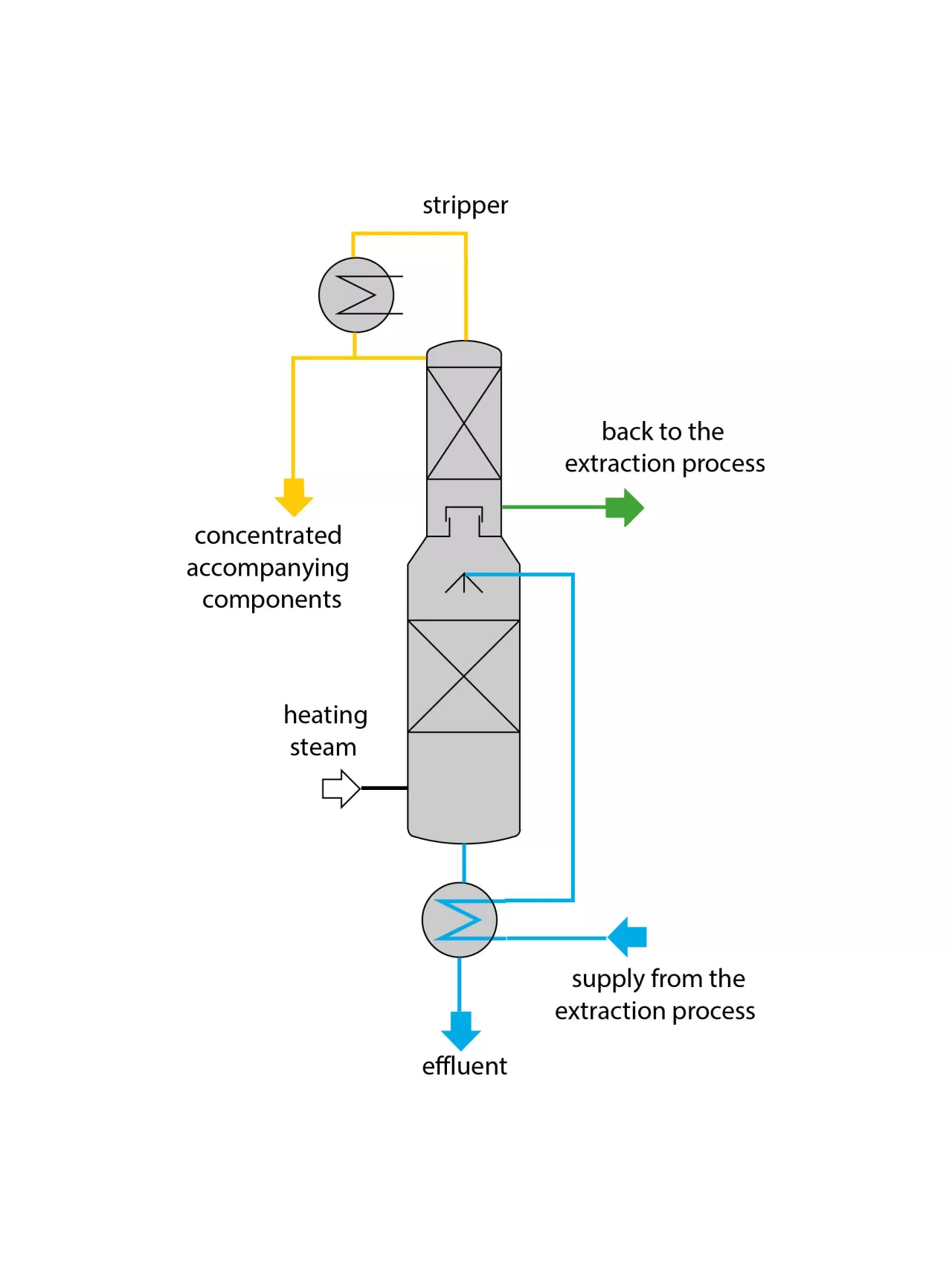
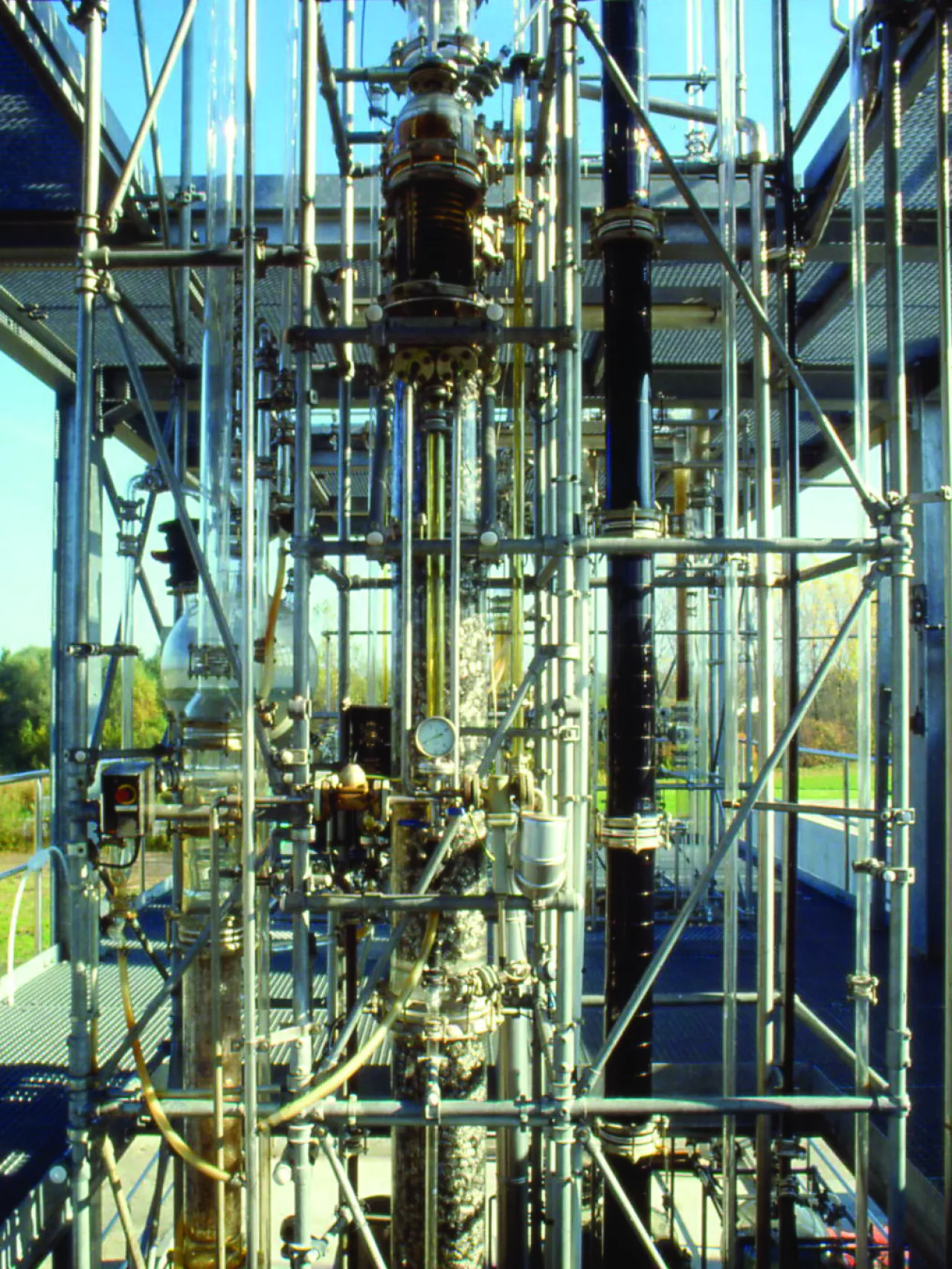
¿Tiene preguntas?
Nuestro equipo está listo para colaborar con usted y proporcionar soluciones para sus proyectos.
Descargue el documento
Solicitar una descarga
Con el fin de procesar su solicitud de folleto de manera eficiente, le rogamos que nos facilite la información requerida a través de nuestro formulario.