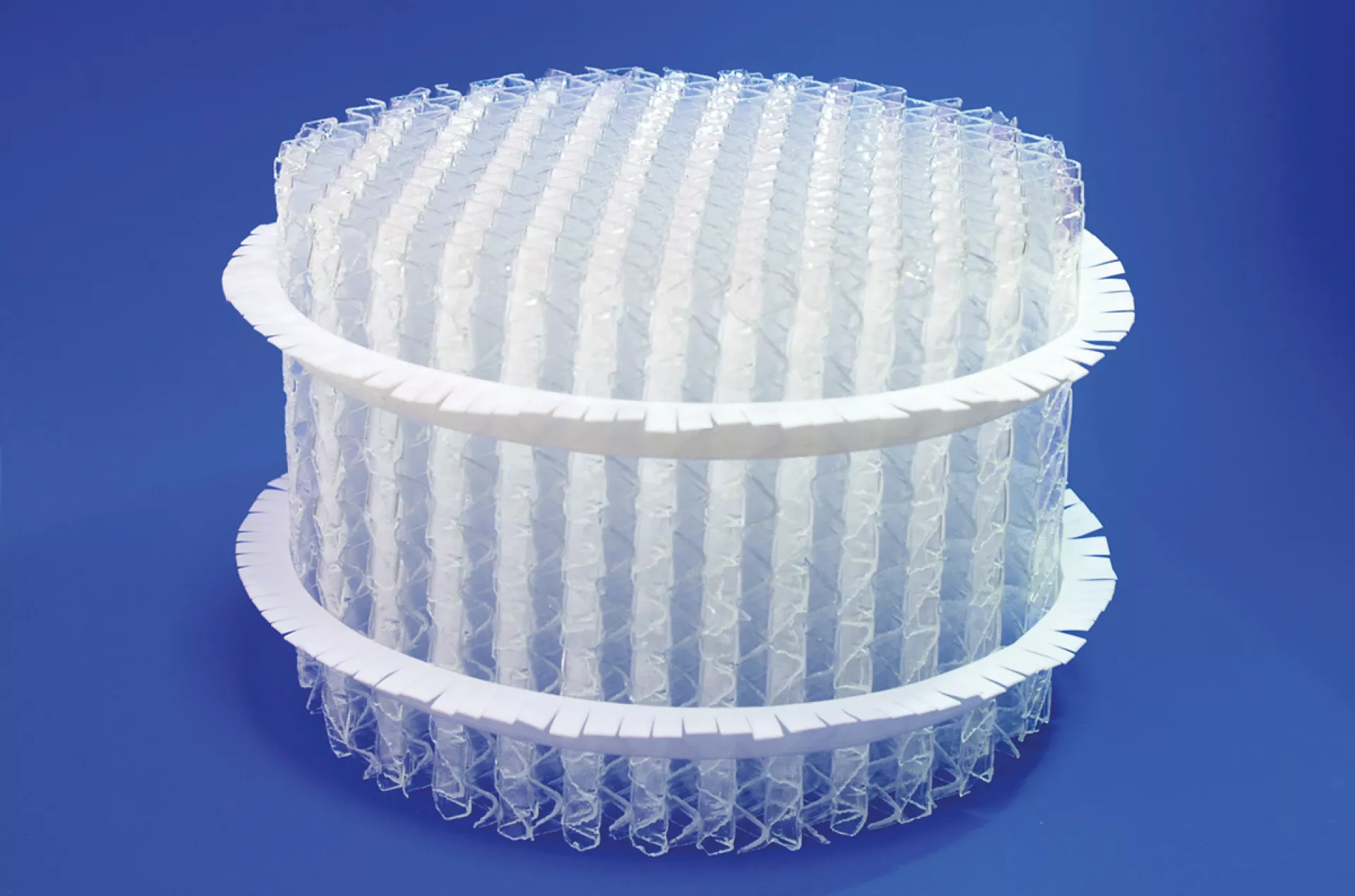
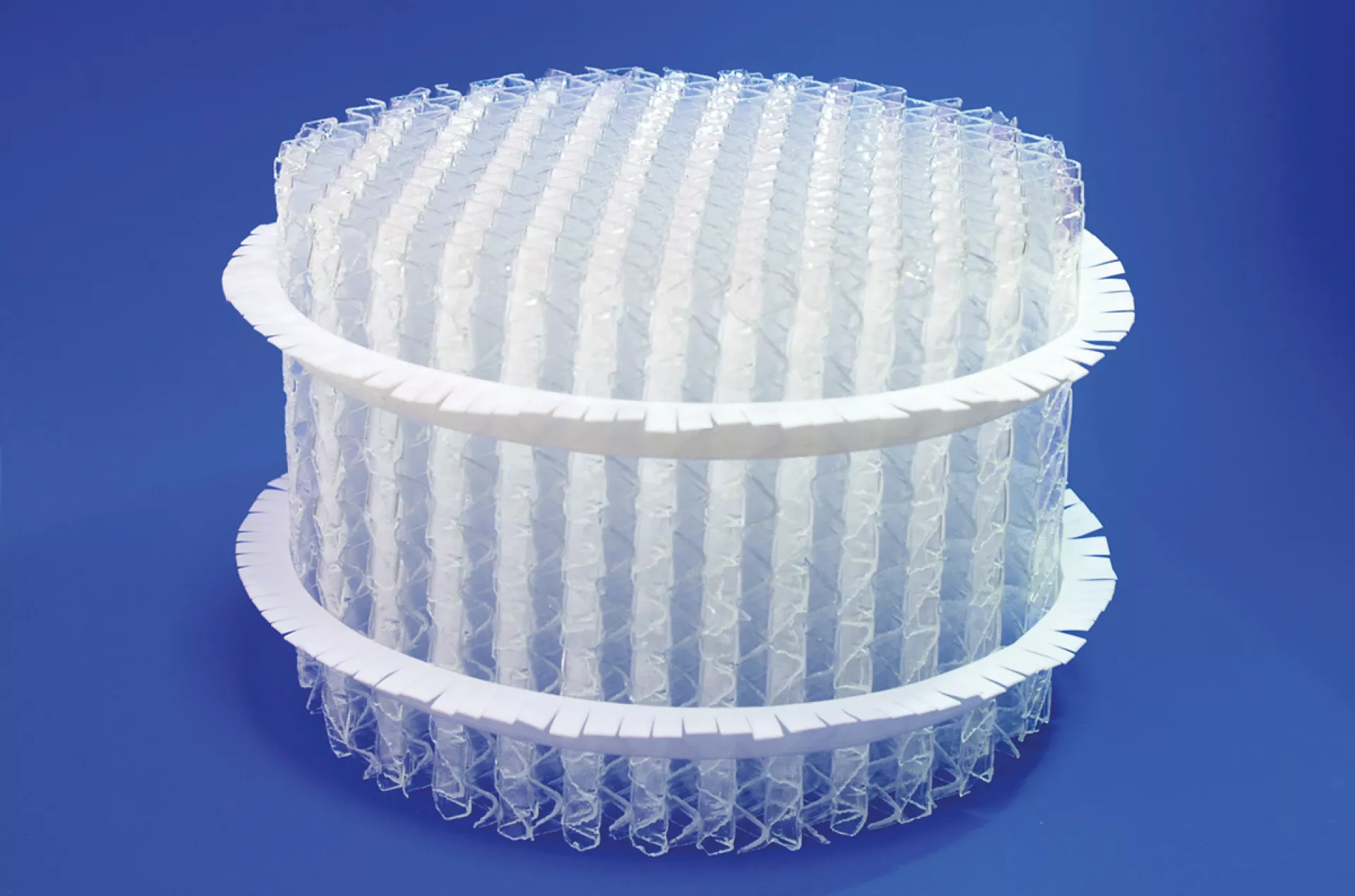
DURAPACK®
La solución eficiente para procesos de separación térmica altamente corrosivos
Los paquetes de reemplazo DURAPACK® patentados están fabricados en vidrio borosilicato 3.3.
El relleno está compuesto exclusivamente de vidrio borosilicato 3.3; las placas están fusionadas entre sí sin adhesivos, de modo que únicamente el vidrio borosilicato 3.3 entra en contacto con el medio a procesar.
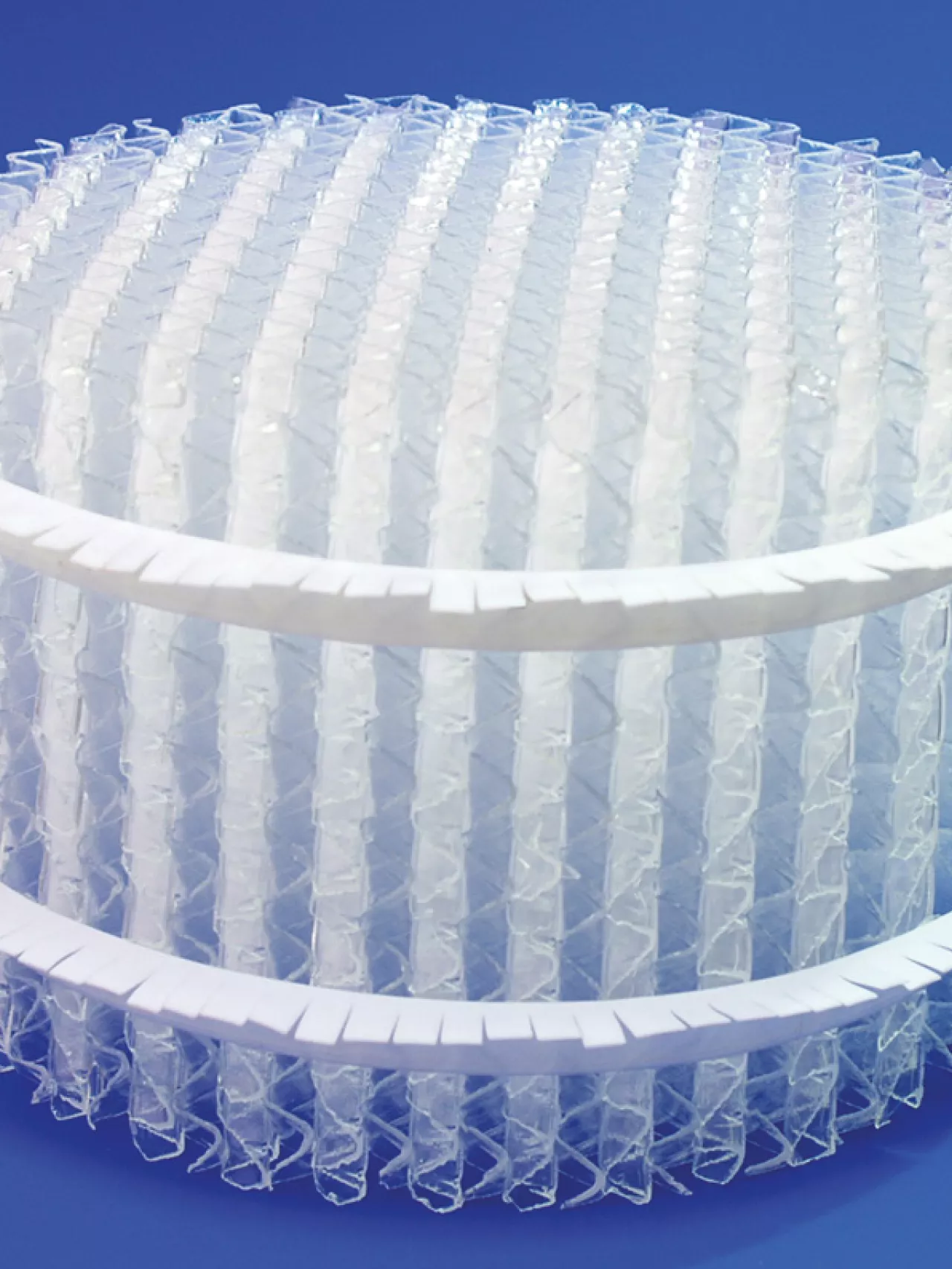
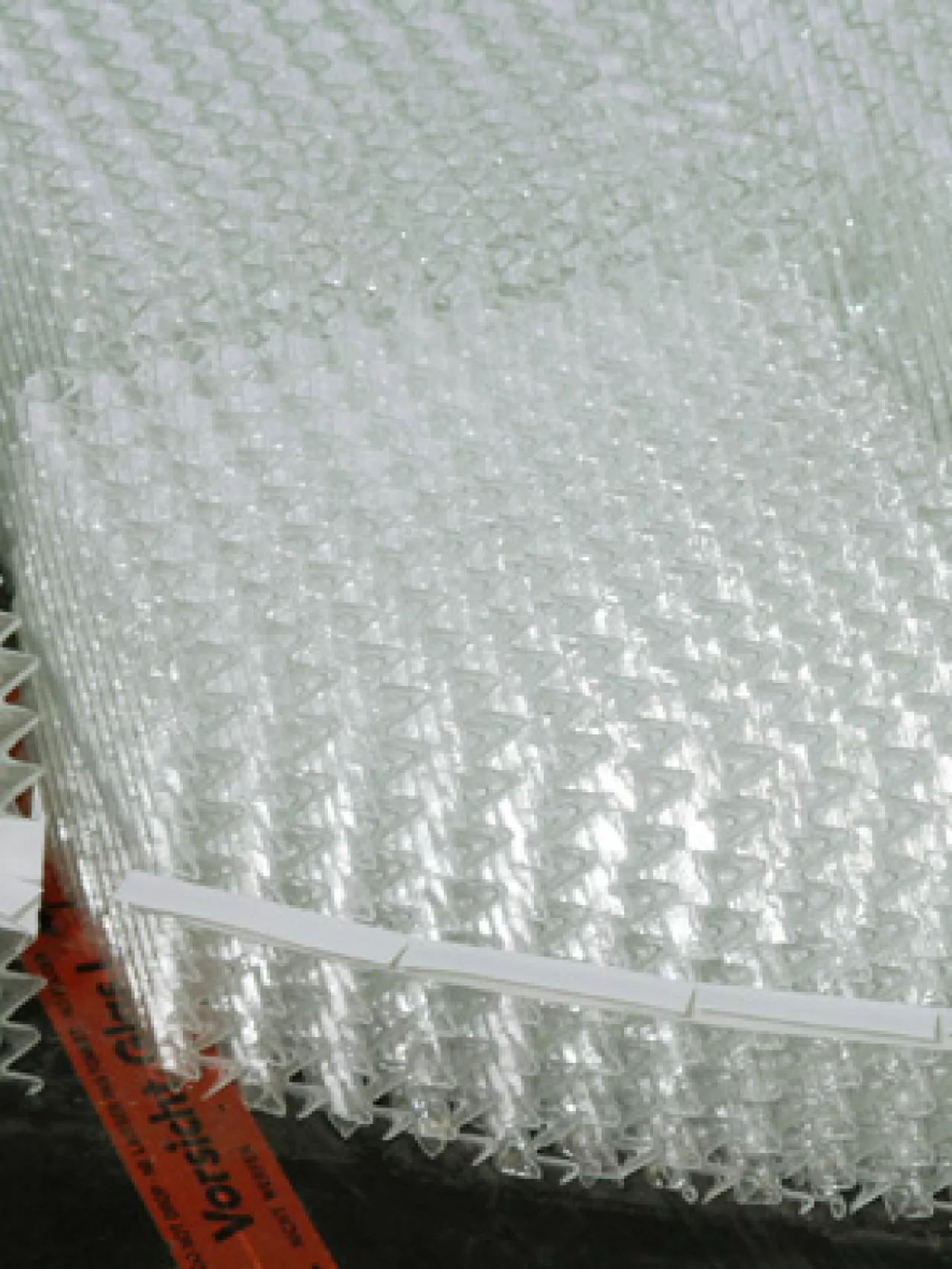
Relleno estructurado DURAPACK®
- Fabricado en vidrio borosilicato 3.3
- Alta resistencia a la corrosión
- Elevada eficiencia de separación
- Baja pérdida de carga
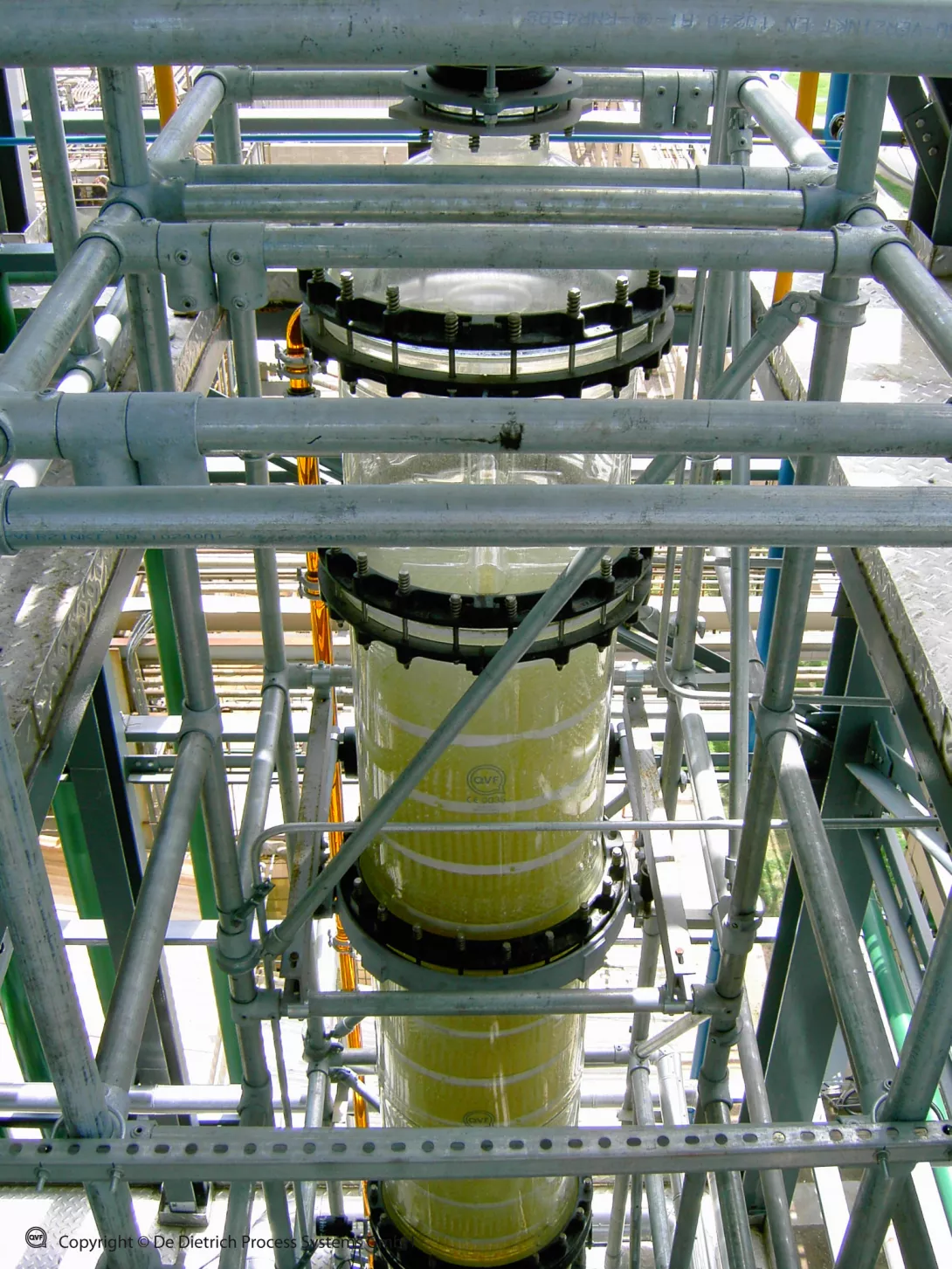
DURAPACK® es la solución eficiente para la separación térmica de medios altamente corrosivos. Su diseño patentado en placas onduladas de vidrio borosilicato 3.3 sin adhesivos garantiza una alta superficie de transferencia de masa, baja pérdida de carga y resistencia química máxima.
Ideal para procesos de absorción, desorción, destilación y extracción con ácidos minerales (H₂SO₄, HNO₃, HCl) y halógenos (Cl₂, Br₂, I₂), donde metales y plásticos no son adecuados.
Superficie lisa, inerte y fácil de limpiar para un funcionamiento seguro y duradero.
Deflectores de pared (Wall Wipers)
Tiras de PTFE para mejorar la eficiencia
En las columnas con relleno, el líquido tiende a escurrirse por las paredes internas sin mojar el relleno, lo que reduce la eficiencia de la transferencia de masa. Para evitarlo, los deflectores de pared devuelven el líquido al interior del relleno a intervalos regulares.
Hemos desarrollado tiras de PTFE y embudos guía que se integran en los tramos de columna o rodean el relleno estructurado en bandas, optimizando así el rendimiento.
El relleno DURAPACK® puede utilizarse tanto en columnas de vidrio como en columnas de otros materiales (acero vitrificado, recubrimiento en PTFE o tantalio). En columnas de vidrio QVF® hasta DN1000, los deflectores estándar eliminan el espacio entre el relleno y la pared, sin necesidad de tubos de vidrio con perforaciones especiales.
Los elementos de relleno tienen una altura estándar de 200 mm. Bajo solicitud, se pueden suministrar en alturas menores. Hasta DN300 se incluyen dos deflectores por segmento; a partir de DN450, uno por capa es suficiente. Los segmentos DURAPACK® con deflectores flexibles pueden instalarse fácilmente en columnas de vidrio estándar.
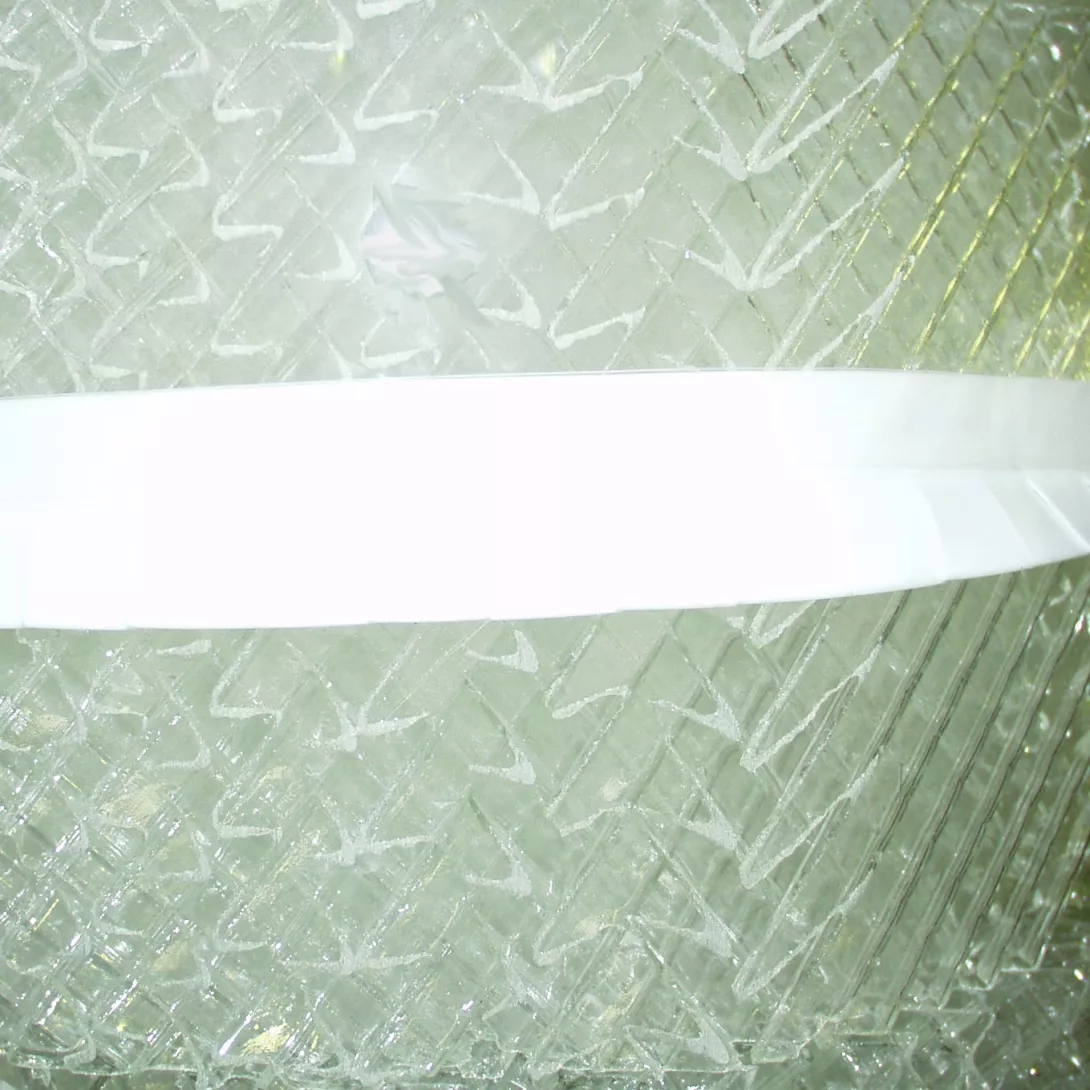
LECHOS DE RELLENO
La altura de los elementos de relleno para todos los diámetros es de 200 mm. Los DURAPACK® con diámetro nominal de DN100 a DN450 constan de un solo elemento, por lo que pueden ser colocados en un anillo de soporte. Los rellenos con un diámetro nominal de DN600 o superior están divididos en segmentos individuales y requieren por tanto una bandeja o rejilla como soporte para el lecho de relleno.
Debido a la segmentación, no hay límites para diámetros mayores. Las columnas de vidrio QVF® están disponibles hasta DN1000. Las columnas esmaltadas de DeDietrich® se fabrican a un diámetro nominal de hasta DN2400. La altura máxima de relleno por bandeja de soporte es de 5 m.
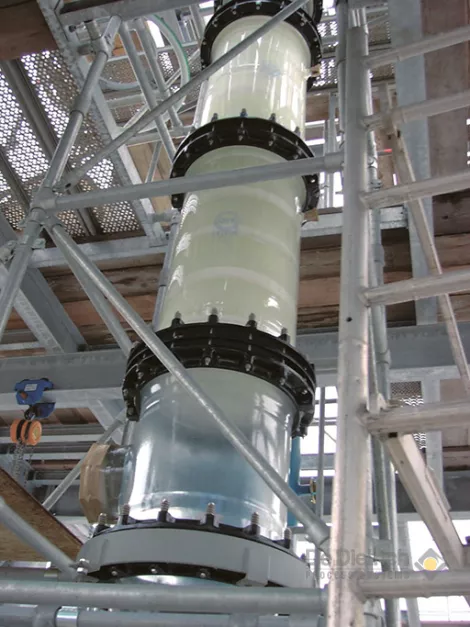
¿Tiene alguna pregunta?
Nuestros equipos están listos para colaborar con usted y ofrecerle soluciones adaptadas a sus proyectos
Descargue el documento
Solicitar una descarga
Con el fin de procesar su solicitud de folleto de manera eficiente, le rogamos que nos facilite la información requerida a través de nuestro formulario.