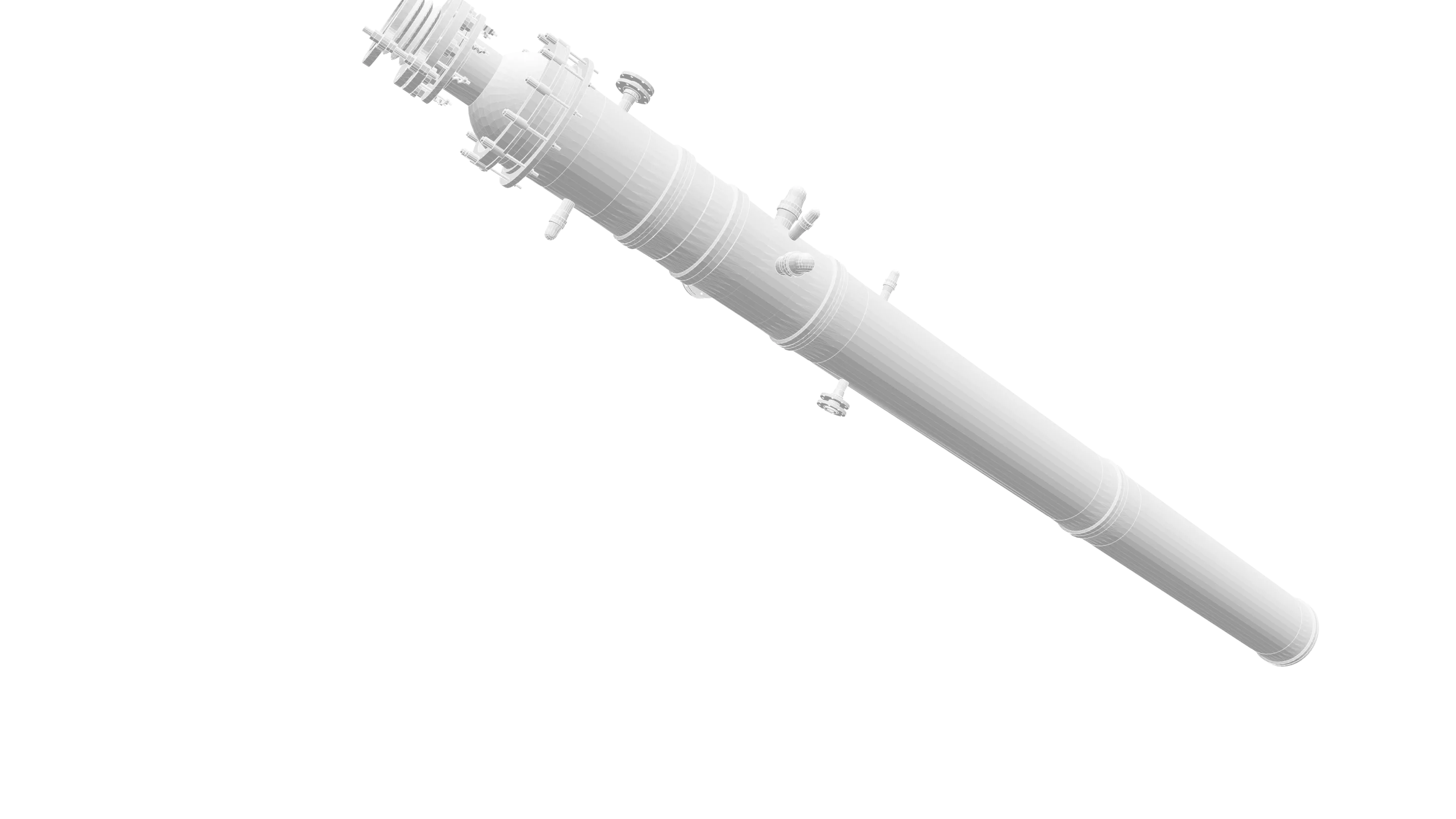
Colonnes en verre
Solutions de procédés pour la séparation thermique
Colonnes et éléments internes pour milieux agressifs
Solutions optimales utilisant des colonnes de séparation pour des procédés hautement corrosifs
Les procédés de séparation thermique sont souvent utilisés lors du traitement et du nettoyage des produits chimiques. Les procédés qui impliquent deux liquides ou un liquide et un gaz sont très courants. Les procédés utilisés impliquent principalement l'extraction, l'absorption, la désorption ou le stripping, la distillation ou la rectification.
Colonnes et éléments internes pour milieux agressifs
Solutions optimales utilisant des colonnes de séparation pour des procédés hautement corrosifs
Les procédés de séparation thermique sont souvent utilisés lors du traitement et du nettoyage des produits chimiques. Les procédés qui impliquent deux liquides ou un liquide et un gaz sont très courants. Les procédés utilisés impliquent principalement l'extraction, l'absorption, la désorption ou le stripping, la distillation ou la rectification comme indiqué dans le schéma ci-joint. Ces procédés de séparation nécessitent un transfert de masse entre deux phases ; dans l'exemple de rectification ci-dessus, le transfert de masse entre la phase liquide et la phase gazeuse. Le fait de maintenir l'équipement utilisé dans ce procédé aussi compact que possible nécessite de créer une surface de transfert de masse maximale dans un volume aussi petit que possible, ce qui implique des colonnes avec des éléments internes spécialisés dans l'ingénierie des processus thermiques
Le coeur du procédé dans les colonnes se compose de garnitures qui fournissent les surfaces de transfert de masse ; elles sont constituées de plateaux spécialisés tels que les plateaux à cloches ou à tamis aussi bien que des garnitures aléatoires ou structurées. Particulièrement, pour les garnitures aléatoires ou structurées et en plus des plateaux de support, d'autres composants internes sont nécessaires pour humidifier, de façon égale, toutes les surfaces pour un transfert de lasse optimal. Ces composants additionnels comprennent des distributeurs de liquide qui distribuent, de façon égale, le fluide entrant sur toute la largeur de la colonne, et des racleurs de paroi pour renvoyer le liquide de la paroi à l'intérieur de la colonne dans le garnissage. D'autres composants internes sont nécessaires pour contrôler le flux de liquide hors de la colonne; des dispositifs antibuée restreignent efficacement la dérive des gouttelettes à l'extrémité supérieure de la colonne, tandis que des collecteurs situés sous les garnitures capturent le liquide de reflux, soit en éliminant le liquide de la colonne, soit en le renvoyant à un redistributeur. Les brise-vortex et les collecteurs à l'extrémité inférieure de la colonne assurent un drainage efficace du liquide. Pour des performances optimales du procédé, les conceptions et les matériaux varient considérablement enfonction des différents procédés et les largeurs nominales des colonnes. Ces procédés QVF® ont été développés depuis des décennies et ont fait leurs preuves.
Nous serions heureux de concevoir une colonne et sélectionner des composants internes optimisés pour votre application.
De l'ingénierie de base jusqu'à la mise en service, nous fournissons le procédé complet.
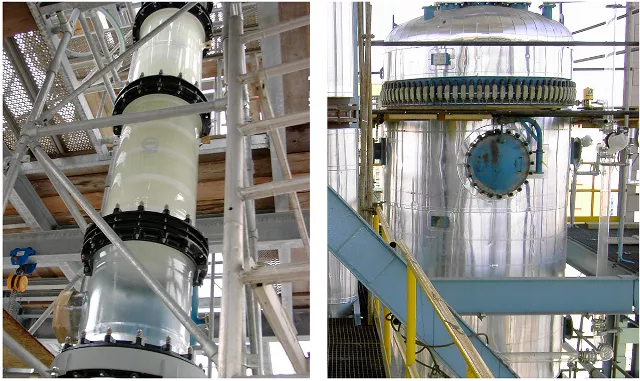
Colonne de séparation
Colonne de verre et d'e-mail
Colonnes de verre Chiffres clés
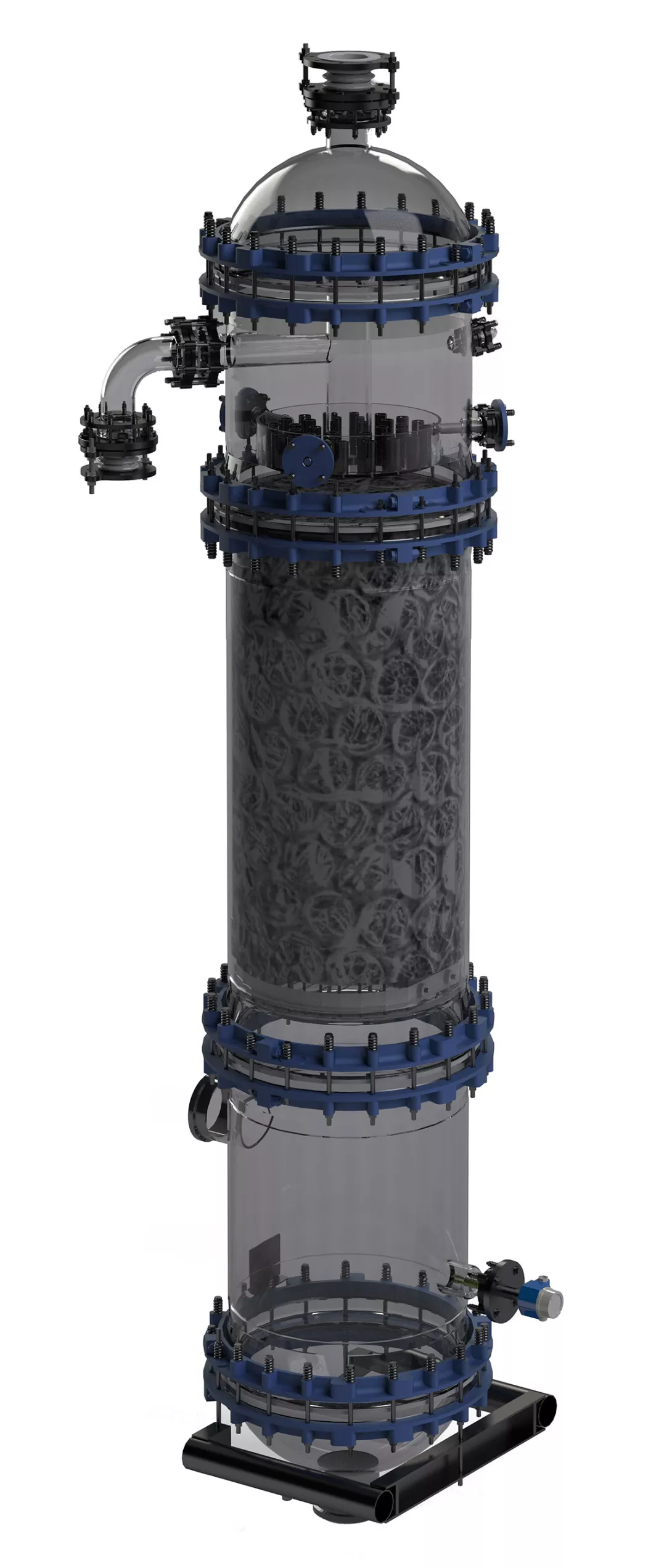
Nos colonnes en verre comprennent :
- Les barquettes à bulles d'air, la solution idéale pour une large gamme de charges
- Emballage, pour une compatibilité garantie
- Emballage structuré pour une grande efficacité de séparation et une faible chute de pression
- Racleurs de paroi / entonnoirs de guidage, bandes de PTFE pour augmenter l'efficacité
- Grilles de support, verre pour transporter l'ensemble de la charge en toute sécurité
- Plateaux à noyaux QVF® brevetés
- Distributeurs de liquide, mouillage uniforme pour toute charge
- Collecteurs pour un drainage latéral fiable
- Démineurs et éliminateurs de brouillard, pas d'entraînement de gouttelettes
- Brise-vortex, collecteurs de sortie, entrée de vapeur pour un drainage fiable
CONCEPT - CONCEPTION - INGÉNIERIE - MISE EN ŒUVRE
Nous possédons des décennies d'expérience dans la fourniture de systèmes de colonnes pour les procédés de séparation thermique, particulièrement ceux impliquant des milieux hautement corrosifs comme des acides. Nous concevons et nous fabriquons les composants principaux selon les normes et les directives de qualité nationales et internationales. Les procédés de séparation ont été développés dans notre propre laboratoire de test. Par conséquent, nous possédons notre propre expertise dans le développement des procédés de séparation et, sur demande, nous procurons des garanties pour le procédé. Nous nous ferons un plaisir de concevoir pour vous, en se basant sur des simulations informatiques, la colonne la plus appropriée pour votre application, une solution optimale pour faire fonctionner votre procédé de façon fiable et efficace.
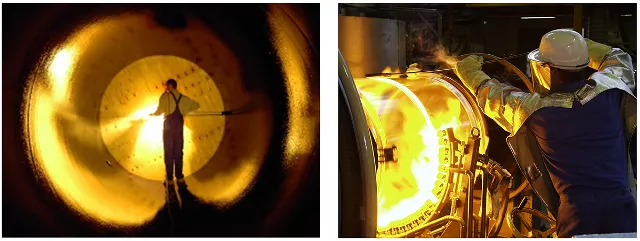
Production d'une section de colonne en acier émaillé / Production d'une section de colonne en verre borosilicaté 3.3
Nous livrons des colonnes en verre Borosilicate 3.3 jusqu'à DN1000 et des colonnes en acier émaillé De Dietrich® jusqu'à DN2400. Nos colonnes fonctionnent à des températures allant de -60 à +230 °C. Nous concevons des colonnes en verre QVF® et des colonnes en acier émaillé De Dietrich® selon les normes et Directives 2014/68/EU (97/23/EC) et AD-2000 ou DIN/EN-13445) pour les appareils sous pression pour le marché Européen et les normes applicables telles que l'ASME VIII Div.1 pour les États-Unis ou le SQL pour le marché chinois des colonnes émaillées. Les colonnes en verre QVF® répondent aux normes EN1595 et sont approuvées pour des pressions allant de -1 à +1 bar, et les colonnes en acier émaillé De Dietrich® sont habituellement approuvées pour des pressions entre -1 et +6 bar. Nous fournissons également des colonnes pour des applications sur demande spécifique.
Les deux matériaux utilisés – l'émail de De Dietrich® DD3009 et le verre borosilicate 3.3 de QVF® – sont extrêmement résistants à l'acide, proposant une alternative rentable et résistante à la température pour des matériaux métalliques spéciaux et la doublure en PTFE non-résistant au vide.
Les surfaces des deux matériaux sont inertes et extrêmement lisses, réduisant ainsi le risque d'agglomération tout en facilitant le procédé de nettoyage. Les deux matériaux sont catalytiquement inertes et neutres au goût.
Notre procédé de fabrication unique assure une précision de tolérance globale dans l'aspect lisse, droit et arrondi. Les colonnes émaillées sont disponibles à des tolérances jusqu'à ½ DIN 28007-T2 sur demande. Notre revêtement émaillé répond aux normes actuelles telles que ISO 28721-1 sur la qualité et l'assurance qualité.
Les hauteurs du plateau, du distributeur de liquide et du collecteur en plus de la hauteur de la section de colonne pour la garnissage aléatoire ou structurée jouent un rôle essentiel dans la hauteur globale de la colonne, qui est souvent restreinte à une certaine valeur pour des raisons structurelles. Nous fabriquons des segments avec une hauteur maximale de 5,5 m pour les colonnes émaillées qui peuvent atteindre une hauteur globale de 52 m.
PROCÉDÉS QVF®
Système pour des applications de procédés hautement corrosifs
Acides minéraux
H2SO4 Récupération
HNO3 Concentration
Nettoyage
Dénitration
HCl Concentration
Dilution
Milieux halogènes et halogénures
Br2 et bromures Production
Cl2 et chlorures Nettoyage
l2 et iodures Élimination
Récupération
Gaz résiduaires
NOx Conversion
SO2 et SO3 Absorption
HCl et Cl2 Réduction
Élimination
Nettoyage
Vous avez une question ?
Nos équipes sont prêtes à collaborer avec vous et à fournir des solutions pour vos projets
Documents à télécharger
Demande de téléchargement
Afin de traiter efficacement votre demande de brochure, nous vous demandons de bien vouloir fournir les informations requises à l'aide de notre formulaire.