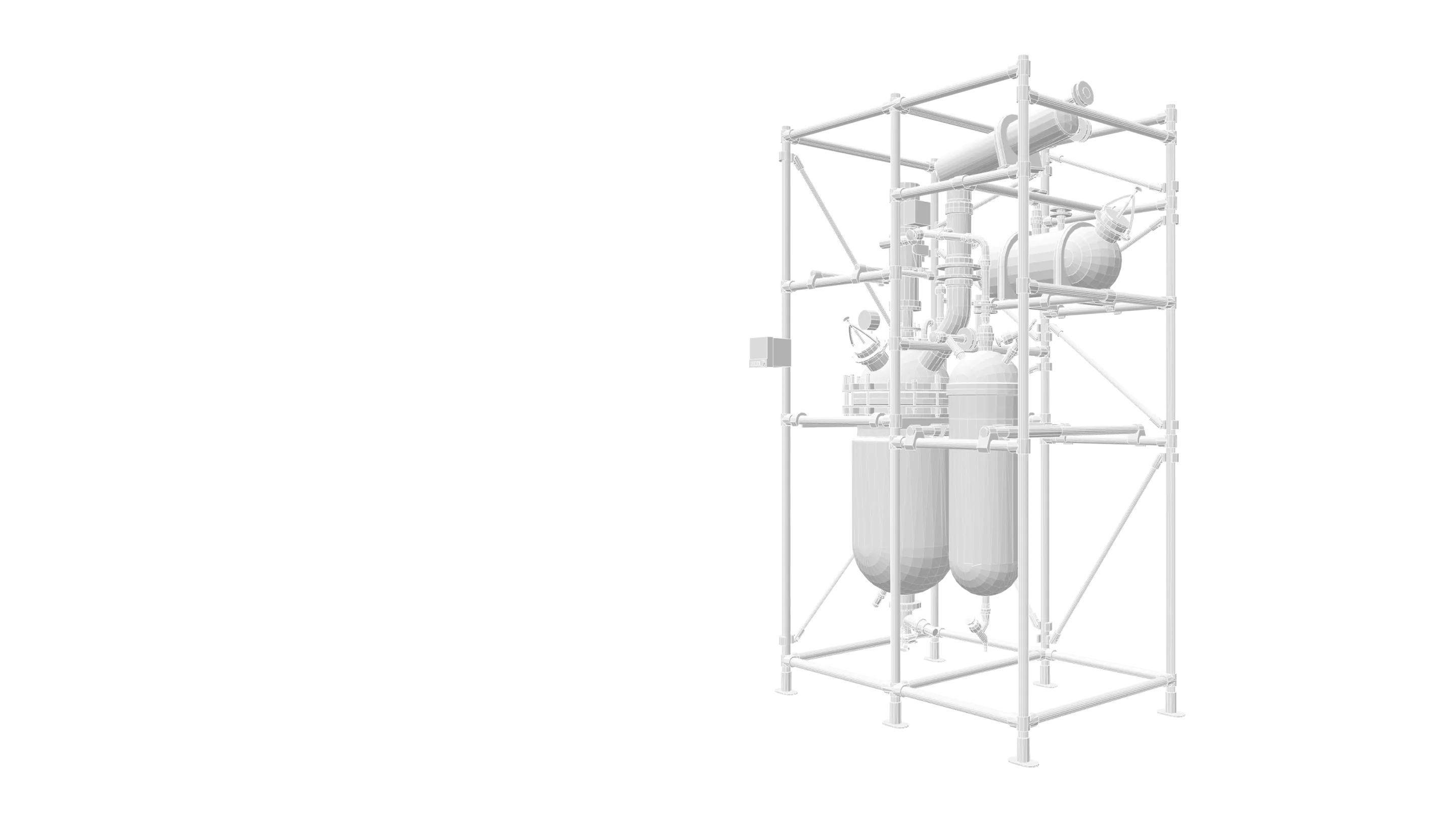
REACTOR UNIVERSAL
El Reactor Universal es la solución cuando hay mayores cantidades que se deben sintetizar que lo que se puede lograr con un matraz de tres cuellos a escala laboratorio.
Upgrade to a complete solution when a 3-neck flask isn't enough
- Reaction unit including instrumentation
- Easy cleaning due to self-draining construction
- Certificates for material in contact with product
- Robust stirrer drive
- For operation in EX-rated areas
Upgrade to a complete solution when a 3-neck flask isn't enough
Universal- Reactor
Complete solution
from borosilicate glass 3.3
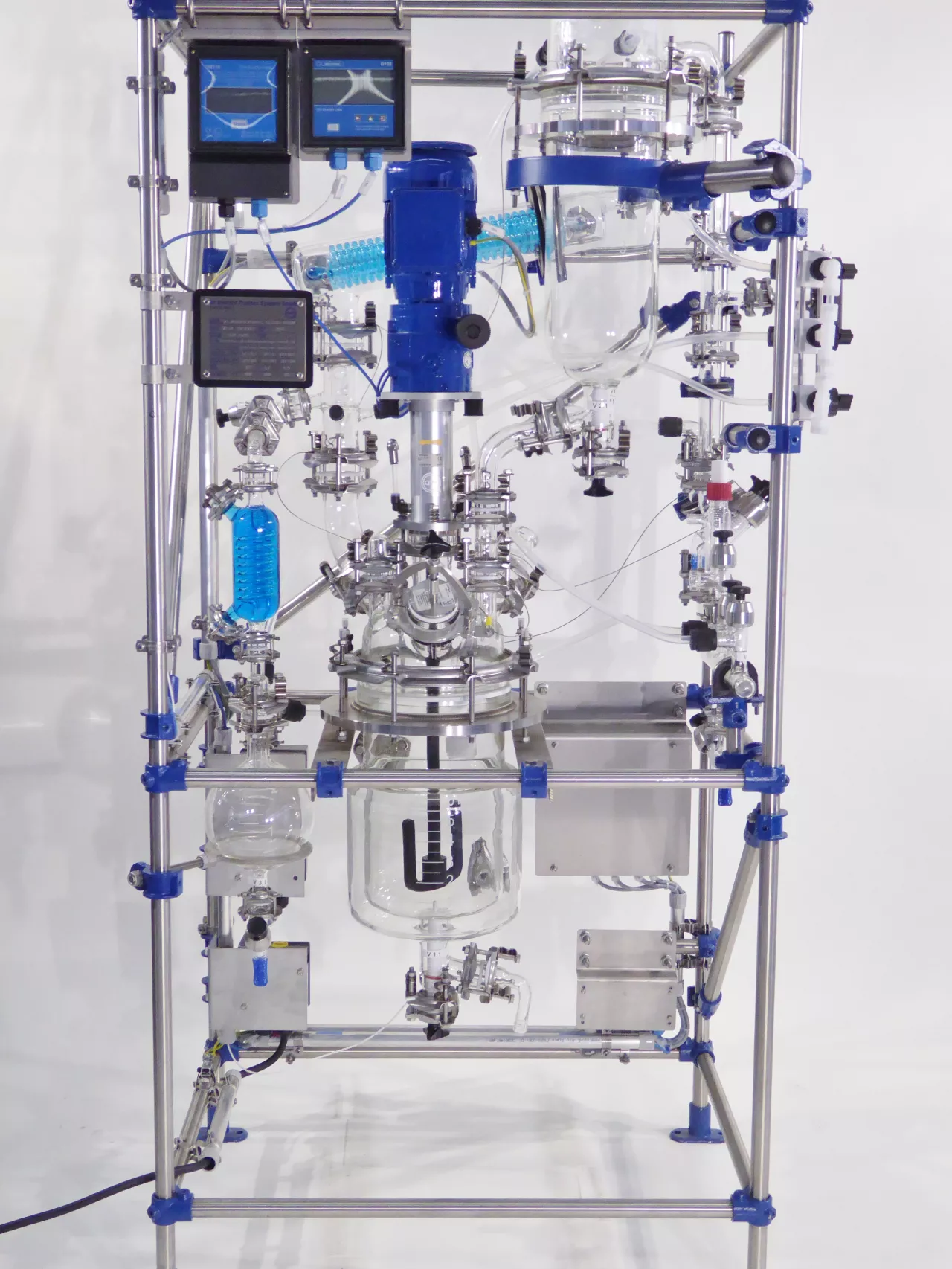
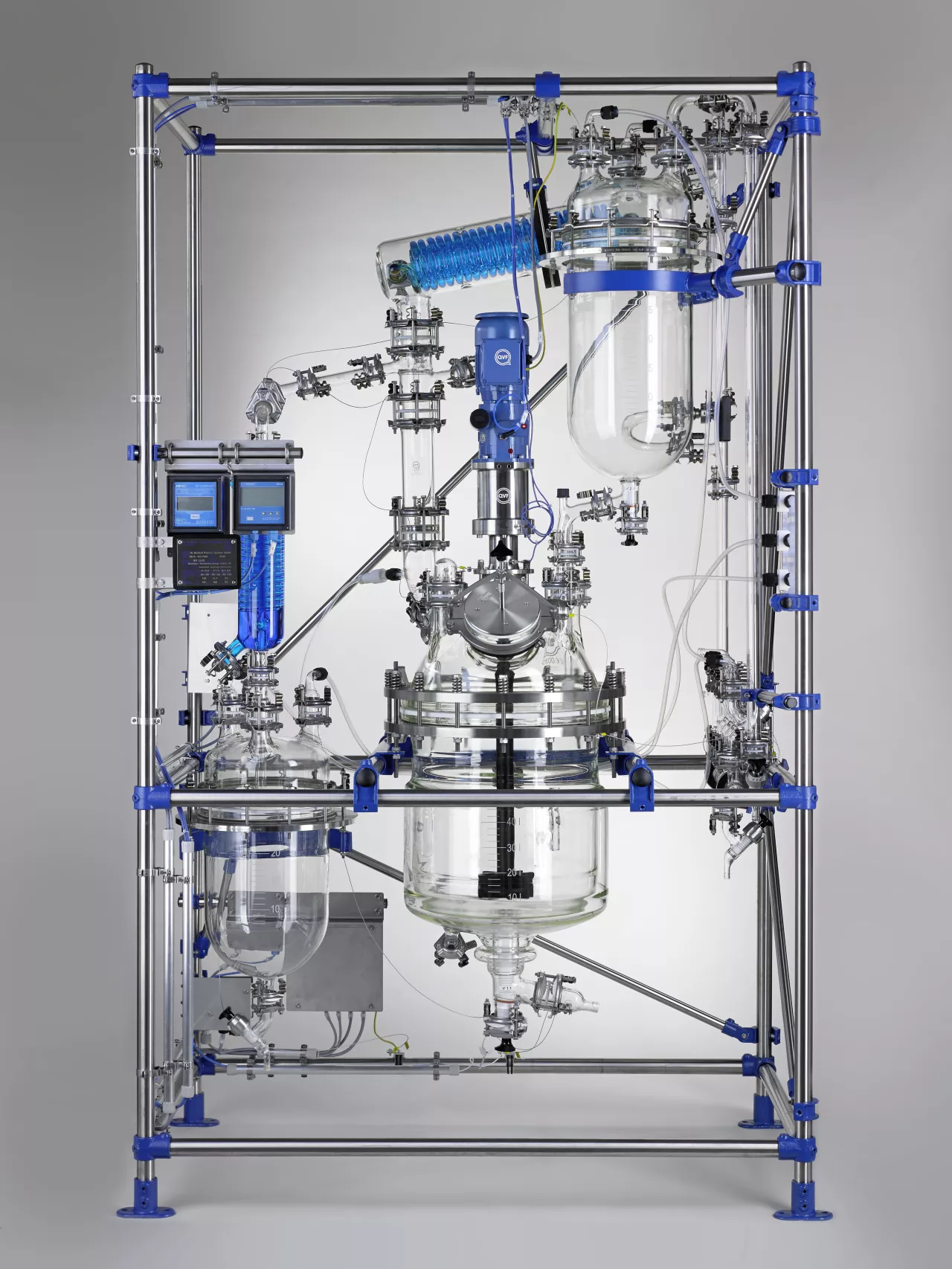
Universal reactor highlights
Concept
The QVF® Universal-Reactor is the solution for synthesizing quantities that are too large for a lab scale 3-neck flask. With this unit it is possible to safely run reactions with larger quantities in the liquid phase under inert gas between -20°C and +150°C. Light boiling components can be distilled off. The QVF Universal-Reactor is equipped with the required instrumentation, ready for operation and only needs to be connected to heating and cooling media. The construction of the reaction unit permits simple and reliable cleaning via CIP-nozzles. The instrumentation of the unit is ex-rated according to German and European regulations so that the complete unit can be operated in EX-rated areas.
Special benefits of our universal reactors range
Standardized up to 50L reactor volume
Easy cleaning due to self-draining construction, certificates for material in contact with product
System includes instrumentation & a robust stirrer drive
For EX-rated areas and processes
Function
The addition of the reactants into the reactor is done through the hand whole equipped with a quick release closure. By applying vacuum to the feed vessel another reactant can be sucked into the feed vessel and afterward dosed through a dip pipe directly into the liquid reaction phase. The valve assemblies permit to operate the complete unit as well as single receivers under vacuum or slight inert gas overpressure up to +0.5barg.
Tempering of the jacketed reaction vessel is done by thermo liquids in a temperature range between -50°C and 200°C. This way the temperature in the reactor, which is captured precisely by a Pt-100 temperature sensor in the bottom outlet valve, can be adjusted below or at the boiling point of the reaction mixture. This permits operation under total reflux or distillation. The mixing process and the heat transfer can be adjusted reproducibly at the continuously adjustable stirrer drive.
The OptiMix® baffle system provides maximum mixing performance without splashing the reaction solution against the inner wall of the reactor. After the reaction solvents or other light boiling components can be withdrawn out of the reactor into the distillate receiver by distillation. Temperature sensitive products can be distilled at lower temperatures under vacuum.
Options
- OptiMix Baffles
- Triple walled reactor
- Triple wall-baffled OptiMix reactor
- Inert gas connection
- Vacuum connection including pressure release valve and bursting disc
- CIP-Nozzle made of PTFE
- CIP-Nozzle made of stainless steel
- RPM-Measurement
- pH-Measurement
- Magnetic coupling
- Safety tub