Rotary Evaporator
- Solvent evaporation -
- Crystallization -
- Drying of suspensions, powders or granulates -
- Various chemical reactions in the liquid phase -
- Ex-rated areas -
- 50 and 100l Evaporation Flasks -
HIGHLIGHTS
- Most universal type of evaporator
- Gentle evaporation due to film evaporation
- Evaporation down to the dry product
- Reducing foam generation due to reduced bubbling
- Avoiding hazardous bumping boiling
- Reliable industrial design
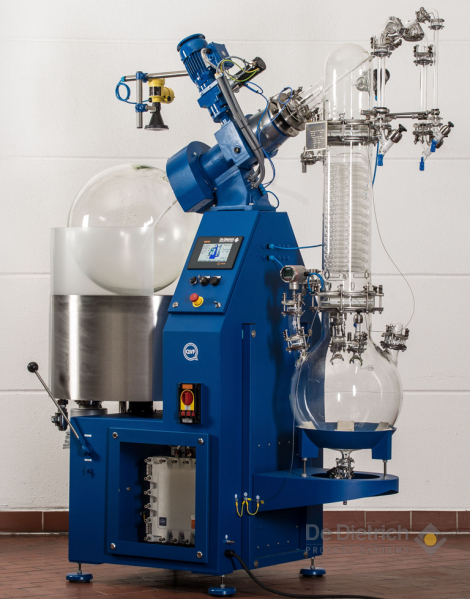
Concept
Rotary evaporators are mainly used to evaporate light boiling components under normal pressure or vacuum. When used in pilot plant and small scale production they are also suitable for semi-continuous evaporation. They are characterized by providing a gentle thermal treatment for temperature-sensitive mediums and provide a higher evaporation rate as non-stirred glass distillation flasks. Compared to other evaporation processes the unique process feature of rotary evaporators is their ability to evaporate all volatile media providing at the end a dry product in the flask.
The process conditions are limited by the maximum temperature of the heating bath ( max. ~ 160°C) , the temperature of the cooling liquid (e.g. ~ 15°C tap water) for the condenser and the vacuum generator ( e.g.~10mbar).
The QVF® ROTADEST can be supplied for EX-rated areas up to zone 1 IIB.

Function
The liquid to be processed in the rotary evaporator is either charged batch wise by gravity, by a pump or sucked-in by vacuum into the evaporation flask. During the evaporation process further feed can be added by means of a pump, gravity or by the operating vacuum through the PTFE-hose passing the rotating shaft and ending in the spherical vessel. The rotating sphere is half way rotating through the liquid in a heating bath filled with water or another suitable liquid heating fluid. The bath is heated by means of electrical heating elements and can be lowered to immediately stop the evaporation process.
The rotation of the sphere which is flanged to the geared motor ensures an effective mixing of the product inside the vessel and wets the complete inner surface of the sphere, increasing the evaporation surface, therefore increasing the evaporation rate and hence shortening the evaporation time.
The components with the lower boiling point are evaporated in the rotating sphere first.Their vapours flow through a sleeve shaft integrated in the drive and enter the condenser assembly. The vapours are condensed and optionally cooled in an distillate cooler before being captured in a final distillate receiver.
Technical description
HEATING BATH
The 50l and 100l rotary evaporators are supplied with a height adjustable heating bath. This heating bath is raised and lowered by a hydraulic cylinder which is operated by means of a hand pump and a pressure relief valve. As a safety feature the bath will be automatically lowered via a solenoid valve in case of a power failure or shutdown. The heating bath is heated electrically. Either water or other thermal oils can be used as a bath liquid. A transparent splash protection keeps back the bath liquid entrained by the rotation of the sphere and prevents at the same time the operator from accidentally touching the optional hand-hole nozzle of the rotating sphere.

Rotating spherical flask
The rotating spherical flask of 50 or 100l is made of corrosion-resistant material borosilicate glass 3.3 permitting an excellent observation of the evaporation process. The level inside the rotating can flask can be monitored with a RADAR-sensor. To further intensify the mixing and for powdery substances the rotary sphere can also be supplied with inwards raised indentations. The sphere is connected to the drive by means of flap screws in order to facilitate their removal. The glass spheres are optionally equipped with a hand hole with a quick relase cover to enable the addition of products directely into the sphere while being fixed to the drive.
Empty line to generate full width
Drive
The glass sphere of the QVF® ROTADEST is mounted to a PTFE-lined steel shaft which is connected to a gear box directly driving the rotating shaft. The gear box permits the stepless adjustment of the number of revolutions of the sphere and can be actuated by an electric motor. Optionally and alternatively an electric motor with frequency converter can be provided. The rotating PTFE-sheeted vapour shaft is sealed by a mechanical PTFE/ceramic-seal at the upper end permitting the reliable operation for slight overpressure or low vacuum. All rotating parts including the connection flange of the rotary sphere are protected by a safety cover.

Condensation section
This module is the complete condenser part in which the condensate is condensed and collected. It essentially consists of a condenser with or without an after cooler, one or two recipients, the connecting pipes, including the necessary fixing as well as a vacuum connection. The condenser part is supported by a console attached to the housing. Condenser parts have already been designed and delivered in a variety of different models to cater to the special desires of the user. However, experience has shown that a wide field of application is covered by the varieties described below. They all have product feeding, concentrate and distillation extraction, connections to cooling water and vacuum as well as a ventilation and pressure measurement connection.
Condenser Version 1
This condenser arrangement with integral spherical receiver has single vacuum, venting and drain connections fitted with valves. The vacuum connections is equipped with a bellows via tee-piece for connection to both vacuum pump and pressure gauge. There is also a facility for filling and suction emptying the rotating flask. This arrangement is supported by means of a bracket fixed to the cabinet.
Rotary film evaporators incorporating this type of condenser arrangement are suitable for continuous operation at atmospheric pressure or batch operation under vacuum.
Version 1


Condenser Version 2
This version is basically the same as option 1 but utilises a standard condenser. This system is fitted with two spherical receivers, therefore allowing one to be exchanged, enabling continuous operation under vacuum as well as atmospheric pressure. The vacuum connection in this system is fitted with bellows to the unit.


Condenser Version 3
This system incorporates a uprising condenser and product cooler for particularly high cooling performance and continuous operation under vacuum. The alternately drainable receivers permit continuous operation under vacuum as well as under atmospheric pressure.
Version 3

Empty Line to generate FULL WIDTH
Measuring and control equipment
The rotary evaporators are equipped with all necessary instrumentation to enable easy and safe operation. The operating touch panel is positioned for the convenience of the operator on one side of the upper housing part and permits full control over the process including data logging. All electronic equipment consists of standardized industrial components ensuring long term serviceability. The service access is eased from outside by a removable cover. Explosion-protected versions have an EX-proof sealed EX-housing inside the cabinet which itself is designed splash-proof (IP 54 type of protection).
Indicated and/or controlled are the following parameters:
- Head temperature in the condenser with Pt100
- Bath temperature with Pt100
- Vacuum with pressure transmitter (option)
- Liquid level inside the rotating flask via RADAR (option)
- Speed of the rotary sphere with hand wheel (remote control as option)
One power supply 230/400 V, 3 Ph, N, PE.
The QVF® ROTADEST can be installed in EX-rated areas up to zone 1 IIB.

Dimensions

Empty line to generate full width
Unit | RD50 | RD100 | |
---|---|---|---|
A | mm | 475 | 525 |
B | mm | 760 | 810 |
C | mm | 1450 | 1550 |
D | mm | 740 | 840 |
Lifting | mm | 320 | 380 |
.
Unit | RD50 | RD100 | |
---|---|---|---|
Volume in flask | l | 50 | 100 |
Rotation speed | min-1 | 0 - 82 | 0 - 82 |
Drive power | kW | 0,37 | 0,37 |
Heating power | kW | 9 | 12 |

Special benefits of the QVF® ROTADEST
- Low vacuum due to high performance mechanical PTFE/ceramic-seal and certified glass flange system
- Mechanical PTFE-seal for slight overpressure or low vacuum
- Exclusive use of corrosion resistant materials as borosilicate glass 3.3 and PTFE for all components being in contact with the product
- FDA-Materials certificates for surfaces in contact with product
- Robust drive unit for the rotary sphere
- Condensation section suited to the process
- Proper observability of the processes
- Reliable and sustainable industrial construction
- Simple operation
- Ex-Protected version available