Cleaning of HCl

Contaminations
Hydrochlric acid may occur as gaseous or aqueuous effluent or product from different sources. Even fresh procured HCl of technical grade may not meet the specification for a dedicated process. Hence there are many cases where cleaning or purifying hydrochloric acid besomes advantageous or necessary. The contaminations in hydrochloric acid are in the majority number of cases the following:
- Other hydrogen halogens as HF, HBr or HI
- Other gases less soluble in aqueous HCl as e.g. SO2 or NOx
- Non-volatile inorganic materials such as salts mineral salts as e.g. halogenides
- Volatile and non volatily organic components
The expenses to remove these contaminations should be as low as possible. This is especially achievable when combining cleaning steps with other process steps in one single unit.
Separation of Non-Volatile Contaminations
Non-volatile material contained in hydrochloric acid, such as heavy metal salts, are held back simply by evaporating the acid. A suitable layout scheme is presented below. Upon existence of metal halides the evaporated hydrochloric acid will contain parts of the corresponding hydrogen halides. The metal salts remain in the residue.
Cleaning of HCl by evaporation
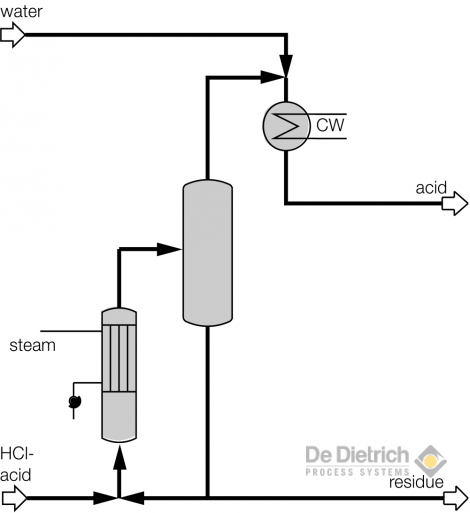
An extra opportunity for separation unfolds a combination of an evaporator with a rectification column and a gasous withdrawal above the lowest packing. This way a waste HCl mixture can be split into water, azeotropic hydrochloric acid and higher boiling components as e.g. HNO3. This is especially interesting if a pre-concentrationing step is necessary for the overall process anyway. Here, the concentration is combined with the cleaning process.
Cleaning by rectification

Separation of Organic Materials and Absorbed Gases (e.g. SO2)
In case the incoming HCl waste gas stream also containes volatile components which are less soluble in water than HCl they can be stripped off in the same column. Examples are gases as like SO2 or organic substances which are either light boiling as e.g. acetone or non-misible in water as e.g. toluene. HCl is absorbed in the upper part of the column increasing the temperature. Additional steam is introduced from the bottom part of the column stripping off the a.m. components. The uprising vapours are then condensed. If these vapours contain non condensible gaseous contaminations like S02 it can be an uprising condenser whereas a falling condenser is more appropriate for condensible contaminations avoiding the immediate reflux of the condensate back into the column and enabling an optional phase separation.
Separtion of Organics
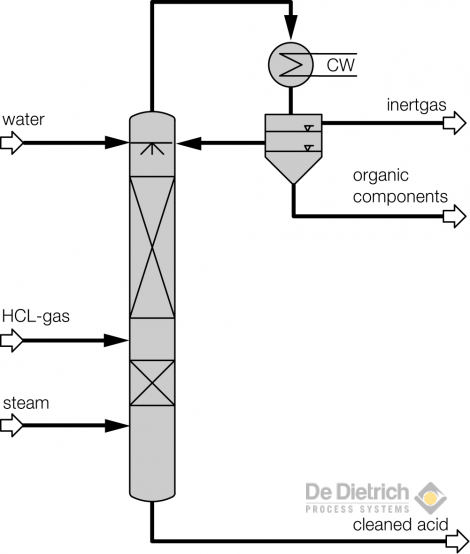
Removal of Bromide Ions
As the natural sources of chlorides contain also bromides hydrochloric acid may also contain hydrobromic acid.Depending on the amount of bromides the target is either just the removal or in case of higher bromide content the recovery of bromine. The bases of the removal of the bromides is their oxidation to volatile bromine which can be stripped off. The most commonly used oxidizing agent is chlorine.
Separation of bromine

The debromination requires as above a stripping process which can be combined with a pre-concentration of the hydrochloric acid to produce azeotropic acid as shown below.
Removal of Bromides Combined with HCl Pre-concentration

Separation of Fluoride Ions
The presence of flourides in hydrochloric acid can be unfavourable for the further use of the hydrochloric acd and is especially disadvantageous when using equipment made of borosilicate glass or glass lined steel. The removal of flourides is simplified by the fact that CaF2 has a very low solubility and CaCl2 has a very high solubility in aqueous HCl. Accoringly by the addition of Ca-salts like CaO to flouride containing aqueous HCl the flourides are precipitated as CaF2 and can be separated from the acidic suspension. The Ca containing hydrochloric acid is then fed to a rectification column as above so that gaseous azeotropic hydrochloric acid can be withdrawn above the evaporator. The residue containing Ca-salts is partially fed back to the precipitator and partially withdrawn from the system. The Ca-loss is compenstated by the addition of CaO. The higher the amount of Ca in the precipitator the lower is the remaining flouride concentration which can be reduced down to very low values. This patented QVF® process (European Patent EP 0506050, German Patent No. 4110177), makes the removal of fluoride ions from hydrochloric acid easily possible, so that cleaned hydrochloric acid can be forwarded for further industrial use.
QVF® Process to Separate Fluoride Ions from Hydrochloric Acid

As CaCl2 is also used as extractive agent to manufacture over-azeotrope hydrochloric acid significant advantages can be achieved when combining the deflourination with this concentration process.